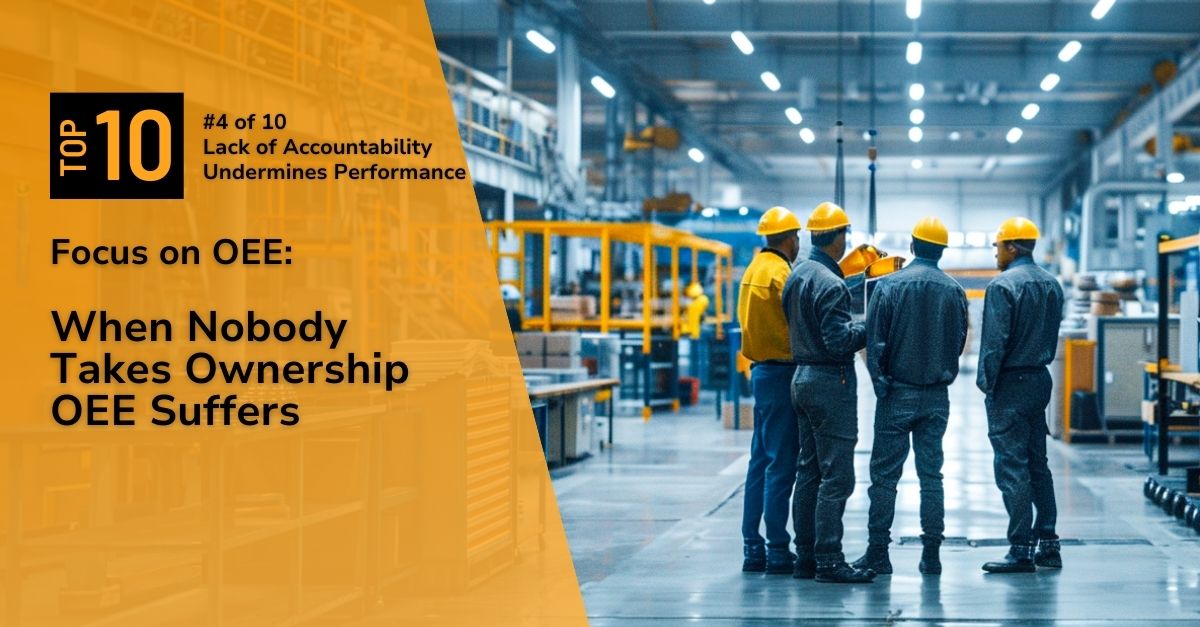
In any organization, accountability is the bedrock of success. When individuals and teams take ownership of their responsibilities, goals are reached, problems are solved proactively, and a culture of continuous improvement thrives.
Conversely, a lack of accountability breeds a cascade of negative consequences that ripple across all aspects of performance.
In the manufacturing realm, the impact of poor accountability directly undermines Overall Equipment Effectiveness (OEE), a critical metric for understanding your production system’s efficiency.
These hidden issues erode your OEE score and compromise your overall production potential.
In this installment of our OEE Mastery Series, we’ll expose the top 10 ways lack of accountability undermines manufacturing performance. We’ll delve into the real-world scenarios plaguing shop floors and provide actionable strategies to restore accountability and drive OEE excellence.
1The “It’s Not My Job” Syndrome:
This attitude creates blind spots. Operators might ignore a sensor misalignment, a loose bolt, or a strange noise if it falls outside their narrowly defined responsibilities. These seemingly minor issues snowball into breakdowns and quality defects.
Mitigation: Nurture a culture of proactive problem-solving. Establish ‘zones of responsibility’ while emphasizing that everyone is accountable for overall equipment health. Reward those who go the extra mile, even if addressing an issue is technically outside their role.
2Tolerance for Recurring Micro-Stoppages:
A sensor misfire that takes 20 seconds to reset seems trivial. However, over a shift, these micro-stoppages accumulate significant lost production time. Desensitization leads to acceptance rather than focused elimination.
Mitigation: Implement an ‘andon’ system for micro-stoppages. Enable operators to quickly signal for help. Use data to identify the most common culprits, empowering teams to find permanent solutions and reduce their frequency.
3The “Blame Game” Culture:
When a problem arises, does the focus fall on finger-pointing or finding the root cause? In an environment steeped in blame, morale suffers, collaboration breaks down, and troubleshooting becomes reactive and repetitive.
Mitigation: Emphasize that mistakes are learning opportunities. Adopt structured problem-solving techniques like the ‘5 Whys’ or ‘fishbone diagrams.’ Celebrate teams that successfully prevent problem recurrence, not just those that heroically fight fires.
4“Hero Mentality” Dependence:
Having a few go-to experts can be reassuring, but this model breeds bottlenecks and knowledge gaps. When the ‘hero’ is busy or off-shift, problems linger, compromising OEE.
Mitigation: Standardize troubleshooting procedures. Use knowledge-sharing systems to capture insights from experienced personnel. Provide targeted training to upskill the broader workforce, reducing the reliance on a select few.
5Limited Operator Ownership:
Operators treated as mere cogs in the machine become less invested in equipment well-being. They might miss subtle warning signs of impending trouble, opting for reactive maintenance over proactive care.
Mitigation: Involve operators in Total Productive Maintenance (TPM) routines. Have them track key metrics like vibration or temperature. Celebrate teams with exceptional uptime records, fostering a sense of pride in their machines.
6The “Pass the Buck” Problem:
Shift handovers are notorious for lost information: “That vibration wasn’t there yesterday,” or “We ran out of that material last shift.” This lack of continuity leads to delays, scrap, and frustration.
Mitigation: Standardize handovers with digital whiteboards or checklists, ensuring critical details are not missed. Encourage cross-shift problem-solving where feasible, building collaboration rather than silos.
7Ineffective Troubleshooting:
Guesswork and “spray and pray” maintenance prolong downtime. When operators aren’t empowered with problem-solving skills and resources, they resort to quick fixes that mask underlying issues and result in recurring failures.
Mitigation: Provide access to equipment manuals and troubleshooting decision trees. Offer training on fault-finding methods like cause-and-effect analysis. Celebrate successes in preventing breakdowns as much as quick recovery.
8Misaligned Incentives:
Bad habits can take root when bonuses are tied solely to output at any cost. Operators might overlook poor quality or run machines near breaking point, sacrificing long-term OEE for short-term gains.
Mitigation: Build a balanced scorecard. Include metrics like first-pass yield, scrap rate, and machine uptime alongside production volume. Make OEE part of every team’s goals.
9Inconsistent Enforcement of Standards:
Whether it’s cleaning protocols, preventive maintenance schedules, or lockout/tagout, inconsistency creates ambiguity. If shortcuts are sometimes tolerated, they become the norm. This leads to equipment wear, unexpected quality issues, and potential safety hazards.
Mitigation: Clearly define and visually display standards. Conduct regular audits with constructive feedback. Tie adherence to standards to performance reviews, making consistency a core expectation.
10Lack of 5S Discipline:
Cluttered workspaces, missing tools, and disorganized materials hinder efficiency and morale. Operators waste time searching, improvised setups lead to defects, and motivation dips in a chaotic environment.
Mitigation: Implement the 5S principles (Sort, Set In Order, Shine, Standardize, Sustain). Make it a daily habit, not a one-time cleanup event. Visually manage tool storage and inventory, ensuring everything has its place and is readily available, minimizing delays.
Conclusion for Senior Operations Leaders
Addressing the insidious effects of poor accountability isn’t a quick fix. It requires a concerted effort to shift mindsets, improve processes, and foster a culture where everyone takes ownership of performance. The journey begins with recognizing the telltale signs explored in this post. Only then can you start systematically chipping away at these OEE-eroding behaviors.
Over time, a genuinely accountable environment generates its own momentum, where continuous improvement becomes the natural state of operations.
How POWERS Can Help
At POWERS, we understand the challenges of building accountability on the shop floor. Our solutions are designed to empower your team and provide insights that illuminate the root causes of performance losses.
- Real-time visibility: Visual dashboards and alerts reveal those hidden inefficiencies that often stem from diffused responsibility. Micro-stoppages, recurring quality defects, and equipment wear become immediately actionable.
- Data-driven decision-making: Historical analysis helps you identify patterns and link specific issues to lack of ownership. This empowers targeted training, process changes, and incentive programs that address the core problem.
- Accountability framework: POWERS helps you establish clear metrics tied to zones of responsibility, team goals, and individual performance. This fosters a sense of collective purpose and reinforces the link between actions and overall OEE success.
If you’re ready to unlock a new era of manufacturing performance fueled by true accountability, POWERS is your key. Take the first step and reach out to us:
- Speak to an Expert: Call +1 678-971-4711 to discuss your specific challenges and goals.
- Email Us: Get tailored insights by emailing info@thepowerscompany.com
- Request an Assessment: Use our online contact form to schedule an in-depth analysis of your operations.
Continue Reading from this Mastery Series
- Part 1 – The Hidden Costs Undermining Your OEE Score
- Part 2 - Dig Deep to Eliminate Inefficiencies that Silently Sabotage Your OEE
- Part 3 – How Guesswork Kills OEE
- Part 4 – When Nobody Takes Ownership OEE Suffers
- Part 5 – When “Pushing Production” Costs You OEE Points
- Part 6 – The Customer Connection: When Dissatisfaction Drains Your OEE
- Part 7 – Death by a Thousand Cuts: How Wear and Tear Steals From Your OEE
- Part 8 – Competitive Disadvantage: The Hidden Enemy of OEE Excellence
- Part 9 – How Missed Opportunities for Improvement Means Missed OEE Potential
- Part 10 – Is Stagnant Innovation Stagnating Your OEE Results