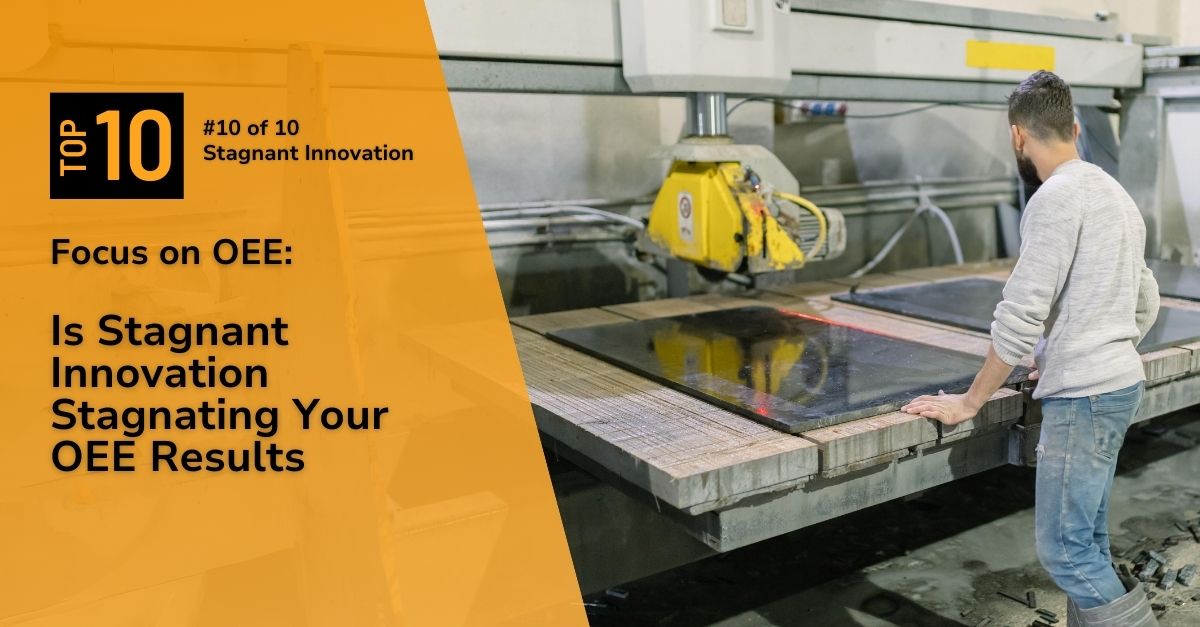
Stagnant innovation is a mindset far more pervasive and dangerous than simply a lack of new technology.
It’s a creeping paralysis that erodes competitiveness within a manufacturing facility. When the drive to continuously improve fades, a host of secondary symptoms start to appear, each chipping away at your Overall Equipment Effectiveness (OEE) score.
Consider a recurring defect occurring at a particular stage in your process. The initial response is to increase inspection after that stage and rework any defective units. This approach merely puts a band-aid on the deeper problem. Without tracking OEE and specifically factoring in the quality losses, the full extent of the issue remains hidden. Your perceived output might remain satisfactory, but you’re expending unnecessary resources on rework.
Stagnant innovation reveals itself when accepting this scenario as ‘just how things are done.’ There’s no drive to ask deeper questions: Why is the defect happening repeatedly? Can improvements at the defect-prone stage prevent it altogether? Is there a pattern behind its occurrence? If tracked meticulously, OEE would expose those quality losses as a prime target for improvement efforts. With such visibility, an innovative mindset pushes for root cause analysis, upstream process optimization, and the eventual elimination of the rework need, leading to a true boost in efficiency.
In this final installment of our Focus on OEE Mastery Series, we’ll expose the top 10 ways stagnant innovation manifests on the shop floor, dragging down your OEE. More importantly, we’ll provide actionable mitigation strategies to put you back on the path toward operational excellence.
1External Contractor Dependence:
When internal problem-solving capabilities weaken, there’s an increasing reliance on outside contractors for repairs and troubleshooting. This has detrimental consequences for OEE: unplanned downtime skyrockets while you wait for contractors to arrive, the absence of hands-on learning for your staff erodes maintenance skills and prolongs future downtime events, and contractor fees are substantial and unpredictable.
Mitigation: Prioritize training programs for maintenance personnel, empowering them to tackle various issues independently. Document recurring problems, solutions, and best practices in a centralized knowledge repository and emphasize predictive and preventative maintenance to reduce reactive troubleshooting.
2Sensor Deficiency:
Insufficient sensors throughout the production line mean you are essentially flying blind with your manufacturing processes. Invisible bottlenecks become evident only after significant performance degradation has occurred, the lack of real-time data makes it impossible to spot subtle trends that could predict impending failures, and response times to deviations or unexpected events are lengthened.
Mitigation: Conduct a thorough audit to identify strategic locations for new sensors, maximizing critical data collection. Integrate the data stream with robust analytic tools to turn raw data into actionable insights and configure alerts to notify operators of potential issues, allowing proactive intervention.
3Undefined Metrics:
The adage, “what gets measured gets managed,” holds true for OEE. Without clear definitions, targets, and tracking of OEE components, it becomes impossible to identify where losses are occurring. Decisions are made on gut feeling, masking real problems within availability, performance, and quality. Chronic micro-stoppages or subtle speed declines go unnoticed due to a lack of focused measurement, and resources are funneled into areas that may not be the root cause of poor OEE.
Mitigation: Calculate true OEE and break it down into its factors. Set achievable goals for each factor with continuous monitoring. Make OEE scores visible on the shop floor, triggering conversations around root causes. Regularly review industry-specific benchmarks to gauge progress realistically.
4Risk Aversion:
Fear of failure stifles experimentation and new ideas. Manufacturing processes stay locked into known solutions, even if they are suboptimal. Performance losses become accepted as ‘the way it is,’ eroding OEE with incremental decrements. Breakthrough ideas that could significantly enhance OEE are never explored, and reliance on antiquated practices persists, hindering efficiency and responsiveness.
Mitigation: Re-frame failures as opportunities, focusing on root cause analysis and preventative action rather than blame. Encourage small-scale pilot projects with clear evaluation metrics prior to full-scale changes and highlight successful innovations, large and small, to build confidence for future ideas.
5Parts Sourcing Issues:
Rigid supply chains and a narrow focus on cost create vulnerabilities. Long lead times for critical parts result in extended downtime when breakdowns occur. A lack of alternative sourcing options leaves you at the mercy of unreliable suppliers, impacting production schedules and overall OEE.
Mitigation: Develop a strategic parts inventory with calculated criticality levels. Expand your supplier network, exploring alternative sources with a focus on responsiveness and reliability. Analyze parts usage data to identify potential future bottlenecks proactively.
6Excessive Inspection:
Over-reliance on inspection as a band-aid for quality issues masks the root cause of defects. This creates bottlenecks in production flow, increases rework time, and consumes valuable resources. Hidden quality problems continue to degrade OEE.
Mitigation: Shift the focus to defect prevention through process improvement initiatives. Implement statistical process control (SPC) methods to detect upstream issues before defects occur. Regularly review inspection points to identify those that can be safely eliminated or streamlined.
7Hidden Rework:
Informal or undocumented rework practices make it difficult to quantify the true extent of quality losses. Rework tasks consume operator time and machine capacity, often undetected by traditional OEE calculations. This hidden drag on OEE persists unless addressed at the root.
Mitigation: Formalize rework tracking mechanisms with clear reporting channels. Analyze rework data to pinpoint recurring quality problems and prioritize those most heavily impacting OEE. Invest in training and process controls to reduce the likelihood of defects at the source.
8Integration Barriers:
Fragmented systems and poor data flow between departments create information silos. This makes it difficult to identify bottlenecks that span functional areas or to make informed decisions based on holistic data. Response times to problems are lengthened, negatively impacting OEE.
Mitigation: Map out the flow of critical information between departments, identifying bottlenecks and redundancies. Invest in software solutions that facilitate seamless data integration across the manufacturing process. Prioritize cross-functional training to promote a holistic understanding of production flow.
9Outdated PM Schedules:
Preventive maintenance (PM) schedules based on outdated assumptions or calendar intervals fail to address the true needs of the equipment. Over-maintenance wastes resources, while under-maintenance leads to unexpected breakdowns. Both scenarios directly erode OEE.
Mitigation: Incorporate condition monitoring technologies for predictive maintenance. Analyze historical failure data to optimize PM intervals based on actual equipment usage. Empower operators with basic maintenance checks to identify potential issues early.
10Change Resistance:
A mindset that resists change, even in the face of declining performance, creates a self-defeating cycle within the manufacturing environment. Operators and managers cling to familiar methods, even when data shows them to be suboptimal. Opportunities for incremental OEE improvements are overlooked or actively dismissed.
Mitigation: Foster a culture of continuous improvement where ideas are welcomed. Tie OEE goals to individual and team rewards, incentivizing a focus on performance optimization. Transparent communication about the reasons behind changes smooths the transition and encourages buy-in.
Conclusion for Senior Manufacturing Operations Leaders
Stagnant innovation is a formidable enemy of manufacturing efficiency. It disguises itself as minor inconveniences, accepted limitations, and a misplaced focus on external factors. However, the damage it inflicts upon your OEE is very real. By recognizing these ten telltale signs and implementing the mitigation strategies outlined, you put yourself back on a trajectory of innovation and continuous improvement.
The journey to OEE mastery is an ongoing one, marked by incremental gains and fueled by a relentless pursuit of eliminating hidden losses.
How POWERS Can Help
At POWERS, we understand manufacturers’ challenges in an increasingly competitive landscape. Our approach to OEE is designed to break down the barriers created by stagnant innovation. We provide:
- Data-Driven Insights: Our advanced analytics platform turns your raw production data into actionable insights, exposing the true cost of downtime, quality issues, and performance bottlenecks.
- Expert Guidance: Our specialists bring deep manufacturing expertise to help you interpret your OEE data, prioritize improvement initiatives, and develop targeted solutions.
- Continuous Improvement Culture: We work with you to instill an innovation-driven, OEE-focused mindset throughout your organization, empowering employees at all levels to champion efficiency.
- Speak to an Expert: Call +1 678-971-4711 to discuss your specific challenges and goals.
- Email Us: Get tailored insights by emailing info@thepowerscompany.com
- Request an Assessment: Use our online contact form to schedule an in-depth analysis of your operations.
Continue Reading from this Mastery Series
- Part 1 – The Hidden Costs Undermining Your OEE Score
- Part 2 - Dig Deep to Eliminate Inefficiencies that Silently Sabotage Your OEE
- Part 3 – How Guesswork Kills OEE
- Part 4 – When Nobody Takes Ownership OEE Suffers
- Part 5 – When “Pushing Production” Costs You OEE Points
- Part 6 – The Customer Connection: When Dissatisfaction Drains Your OEE
- Part 7 – Death by a Thousand Cuts: How Wear and Tear Steals From Your OEE
- Part 8 – Competitive Disadvantage: The Hidden Enemy of OEE Excellence
- Part 9 – How Missed Opportunities for Improvement Means Missed OEE Potential
- Part 10 – Is Stagnant Innovation Stagnating Your OEE Results