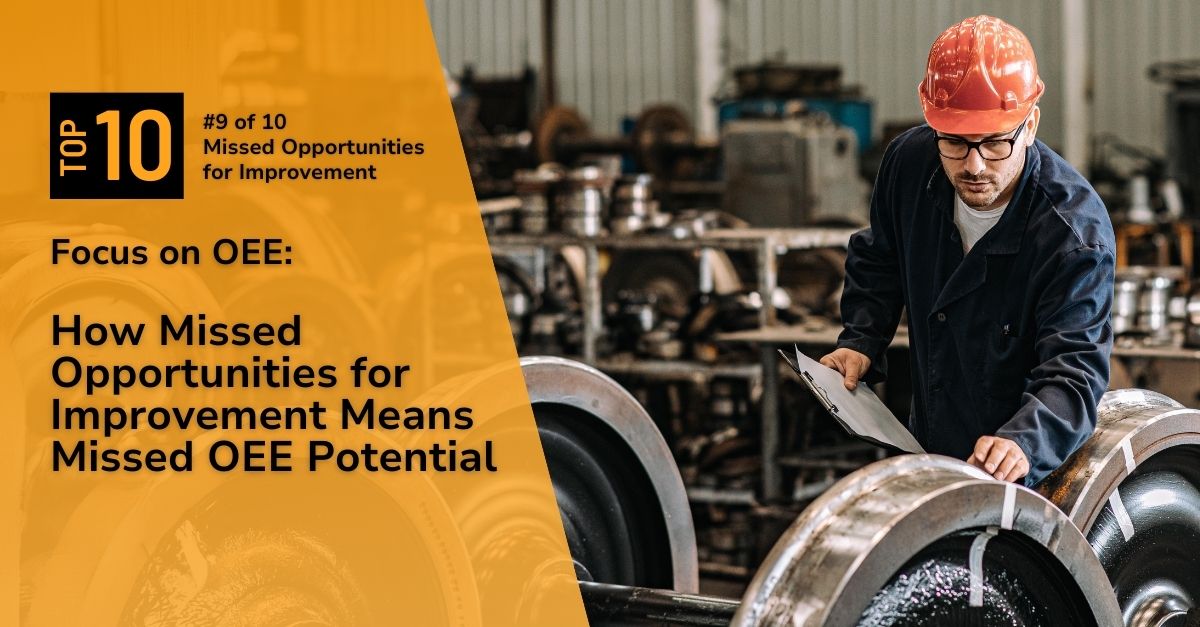
Missed opportunities for improvement are the most subtle threat to your Overall Equipment Effectiveness (OEE). They hide in the gaps between major breakdowns and downtime events, quietly eroding your productivity and profitability.
But it’s these secondary symptoms that are the real culprits. If you aren’t actively tracking OEE, you lack the visibility to identify these hidden enemies. Without that data-driven insight, you risk making decisions based on assumptions rather than facts.
Imagine this scenario: You’re experiencing an uptick in scrap. The initial assumption might be operator error or material issues, driving your OEE quality score down. However, you may miss a more insidious problem without tracking OEE over time. The root cause could be micro-stoppages – tiny hesitations in equipment due to misalignment or insufficient lubrication – slowing your production rate subtly with each cycle. This erodes your performance rate, contributing to the scrap problem without any single, obvious breakdown event to flag it.
In part 9, we’ll expose these OEE threats – the secondary symptoms that are often overlooked. We’ll delve into the nuts and bolts of these issues, sharing real-world manufacturing scenarios and providing practical fixes to regain lost OEE points.
1Unstructured Experimentation:
Haphazard “tweaks” on production lines, without following a structured problem-solving approach like PDCA (Plan-Do-Check-Act) or DMAIC (Define-Measure-Analyze-Improve-Control), waste time and resources. Unrecorded changes make it impossible to understand their true impact. What’s more, this approach breeds a culture where gut-feeling overrides data-driven decisions.
Mitigation: Implement formal scientific methods. PDCA provides a continuous improvement loop for iteratively testing and refining solutions. DMAIC offers a structured, data-driven approach for larger process improvement projects. Train your team in these methodologies to ensure a focused approach to problem-solving, where every change is backed by data, has a clear goal, and is monitored to measure impact on OEE.
2Missing Opportunities for Value Stream Mapping (VSM):
VSM exposes hidden inefficiencies in your production flow. Without this visual representation, identifying the largest contributors to OEE loss becomes a guessing game.
Mitigation: Conduct VSM exercises not as a one-time event but as a regular analysis tool. Look for extended wait times between processes, excessive inventory buildup, or unnecessary transportation steps. These are your prime targets for streamlining efforts that directly boost OEE.
3Over-reliance on Manual Processes:
Manual operations are inherently slower and more inconsistent than automated ones, hurting your OEE’s availability and performance rate. Human error also drags down your quality score.
Mitigation: Start by creating a detailed task breakdown for each operator workstation. Identify repetitive, rules-based tasks that could be candidates for automation. Even partial automation, such as sensor-based checks or automated data entry, can significantly reduce errors and speed up processes.
4Poor Error-Proofing (Poka Yoke) Implementation:
Defects go beyond wasted materials; the rework needed to fix them is a major drain on availability. Poka-yoke aims to make errors impossible, fundamentally shifting your approach to quality.
Mitigation: Don’t just treat the symptoms of defects; attack the root cause. When a defect occurs, use “5 Whys” analysis to drill down into the true cause. Design Poka-yoke solutions that are impossible to overlook – like color-coded parts to ensure correct assembly or fixtures that only allow a component to be installed the right way.
5Minimal Use of Simulations:
Change is inevitable in manufacturing, but making those changes on the live production line can lead to unexpected downtime and quality hiccups. Simulations provide a risk-free digital twin of your processes.
Mitigation: For major line changes, invest in process simulation software. Build a virtual model of your line and test various scenarios like setup time reduction, increased throughput, or new equipment integration. The insights allow you to optimize before implementation, minimizing disruption and maximizing OEE gains.
6Infrequent Gemba Walks:
There’s no substitute for seeing your shop floor in action. Issues invisible from a conference room become glaringly apparent during Gemba walks. This is where you’ll spot micro-stoppages, inefficient workflows, and operator frustrations.
Mitigation: Establish a Gemba culture. Set a cadence for walks that includes managers, engineers, and support staff. Equip them with a checklist not focused on results but on observations—are operators waiting for tools? Are materials placed inconveniently? These granular issues erode OEE over time.
7Ineffective Andon Systems (Visual Alerts):
Andon systems are meant to accelerate problem resolution, yet many fall short. Slow response, unclear alerts, or a lack of problem-solving escalation procedures render them ineffective.
Mitigation: Treat Andon alerts with the same urgency as a fire alarm. Measure and continuously reduce response time. Ensure the alert gives enough information for a first responder to take meaningful action. Don’t let problems linger!
8Inflexible Quality Gates:
Rigid quality checks, especially if placed only at the end of the line, create hidden bottlenecks and foster a reactive quality mindset. When defects pile up before inspection, it becomes a scramble to rework or scrap a large amount of product, impacting your availability and quality metrics.
Mitigation: Shift to in-process quality. Build quality checks into multiple stages. Empower operators to stop the line when upstream issues that could lead to defects are detected. Use statistical process control (SPC) to monitor trends and make adjustments before problems cascade through the line. Early detection and quick resolution protect your OEE by reducing waste and downtime.
9Batching Mentality:
Large batch production seems efficient but hides excessive setup times, and long waits for in-process inventory, and hampers quick reactions to quality issues. Smaller batches may seem counterintuitive, but the OEE benefits often outweigh the perceived downsides.
Mitigation: Challenge the status quo of batch sizes. Use SMED (Single Minute Exchange of Die) techniques to drive down setup times ruthlessly. Explore cellular manufacturing layouts that inherently encourage smaller runs and quicker throughput. The ability to react rapidly – whether to a customer demand change or a quality problem – is far more valuable than it appears on paper.
10Unoptimized “First Pass Yield”:
First Pass Yield (FPY) measures the percentage of products that make it through the entire process without defect or rework. Focusing solely on final quality misses how in-process defects destroy your performance rate and availability, long before they reach the final quality check.
Mitigation: Break down your process into smaller steps. Establish quality checkpoints within the line, focusing on early detection. Train operators to be both producers and quality inspectors for their immediate work area. This mindset promotes problem-solving at the source and prevents a single defect from taking down a whole batch, decimating your OEE.
Conclusion for Senior Manufacturing Operations Leaders
Missed opportunities for improvement lurk within your production lines, slowly but steadily chipping away at your OEE. These seemingly small issues–the micro-stoppages, the overlooked defects, the inefficient workflows—become major hindrances to achieving maximum efficiency. It’s time to stop treating them as part of the daily grind and instead attack them head-on.
Without this insight, you’re shooting in the dark– making changes based on hunches rather than hard evidence.
How POWERS Can Help
At POWERS, we empower manufacturers to achieve their full potential. Our solution is specifically designed to illuminate the path to operational excellence. Here’s how we can transform your approach to OEE improvement:
- Unmask the Hidden: Advanced data collection and analytics expose the smallest events impacting performance. These are the inefficiencies that spreadsheets and manual tracking alone can never reveal.
- Prioritize Your Efforts: With POWERS, you'll identify the missed opportunities with the biggest OEE impact. This laser-sharp focus eliminates wasted effort and ensures your improvement projects yield the maximum return.
- Quantify Improvements: Our platform doesn't just highlight problems; it lets you track and measure the effectiveness of your solutions. Real-time data provides clear evidence of progress–motivating your team and driving long-term success.
- Foster a Culture of Continuous Improvement: POWERS is about more than finding a quick fix. With accessible data and actionable insights, we inspire a proactive, data-backed approach to problem-solving throughout your organization.
- Speak to an Expert: Call +1 678-971-4711 to discuss your specific challenges and goals.
- Email Us: Get tailored insights by emailing info@thepowerscompany.com
- Request an Assessment: Use our online contact form to schedule an in-depth analysis of your operations.
Continue Reading from this Mastery Series
- Part 1 – The Hidden Costs Undermining Your OEE Score
- Part 2 - Dig Deep to Eliminate Inefficiencies that Silently Sabotage Your OEE
- Part 3 – How Guesswork Kills OEE
- Part 4 – When Nobody Takes Ownership OEE Suffers
- Part 5 – When “Pushing Production” Costs You OEE Points
- Part 6 – The Customer Connection: When Dissatisfaction Drains Your OEE
- Part 7 – Death by a Thousand Cuts: How Wear and Tear Steals From Your OEE
- Part 8 – Competitive Disadvantage: The Hidden Enemy of OEE Excellence
- Part 9 – How Missed Opportunities for Improvement Means Missed OEE Potential
- Part 10 – Is Stagnant Innovation Stagnating Your OEE Results