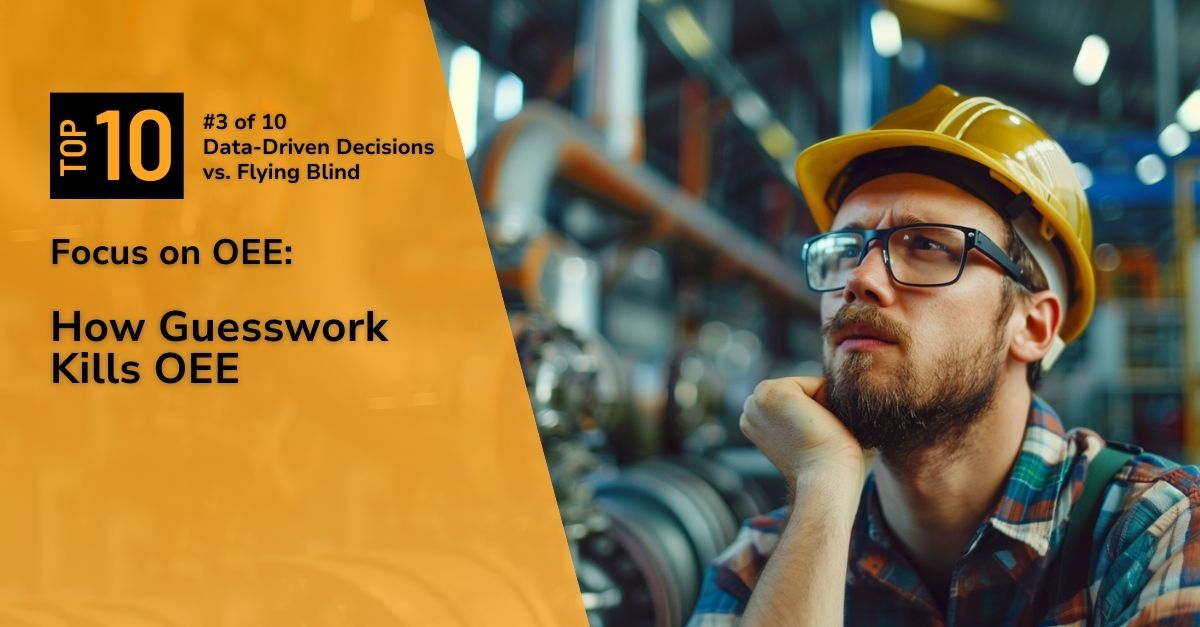
Flying blind – relying on gut feel and guesswork – is a dangerous game on the shop floor. It’s like navigating a complex manufacturing process without a map or compass.
These symptoms manifest as production snags, frustrating inconsistencies, and a nagging sense that your factory could run much more efficiently. They are warning signs that a more profound problem lies beneath the surface. If left unchecked, they undermine your ability to meet production goals, control costs, and deliver reliable quality to your customers.
Let’s break down those symptoms and discuss how to gain the clarity needed for maximum manufacturing efficiency. With data-driven insights, you can transform guesswork into targeted improvement strategies that drive tangible OEE gains.
1Inaccurate Production Capacity Estimates:
Planning teams make promises based on overly optimistic production rates, leading to a mismatch between what’s scheduled and your factory’s true output capability. This results in bottlenecks, strained resources, and a constant struggle to catch up.
Mitigation: Invest in sophisticated capacity planning tools that leverage historical throughput data and factor in realistic constraints like machine setup times, maintenance schedules, and material availability. This data-driven approach prevents overbooking and sets achievable targets.
2Suboptimal Changeover Times:
Lengthy and disorganized changeovers eat away at valuable production time, creating significant losses in machine availability. The longer a machine is idle, the more it erodes efficiency. Moreover, rushed changeovers can lead to errors, jeopardizing product quality.
Mitigation: Employ Single-Minute Exchange of Die (SMED) principles to break down changeover processes into discrete steps. Analyze these steps to identify opportunities for elimination, simplification, or converting internal setup activities to external ones (done while the machine is still running). Train operators extensively on standardized procedures.
3Inaccurate Costing Models:
Misconceptions about the true cost of production distort decision-making. You might underestimate the impact of a high-scrap product line, leading to poor pricing or even continued production of unprofitable items. Inaccurate costing can also mask areas desperately needing OEE improvement.
Mitigation: Replace rough cost estimations with granular activity-based costing. Track labor, machine time, materials, energy consumption, and even indirect overheads across individual product lines or SKUs. This visibility highlights inefficient processes and empowers better pricing strategies.
4Unjustified Equipment Investments:
A tempting but often misguided approach is to throw new machinery at a production problem. New equipment might mask underlying issues without solving them – inefficient workflows poorly maintained older equipment, or inadequate worker training.
Mitigation: Shift your mindset from ‘buy a solution’ to ‘solve the problem.’ Conduct a thorough analysis to find the true bottleneck limiting your output. It might be as simple as reorganizing a work cell or investing in preventive maintenance, yielding a higher ROI than a costly machine replacement.
5Inability to Measure ROI of Improvement Initiatives:
Without establishing a clear before-and-after picture, even successful OEE initiatives can be undervalued. This leads to difficulty justifying future investments, demoralizing the improvement team, and stalling long-term progress.
Mitigation: Measure your baseline OEE (or its individual components) before launching any improvement project. Set quantifiable goals and track the impact of your changes against those metrics. Data-driven success stories create powerful leverage for securing buy-in for future OEE efforts.
6Unrecognized Process Variability:
Unexplained swings in yield, unexpected machine breakdowns, or inconsistent product quality make troubleshooting a nightmare. This variability directly impacts OEE in Availability, Performance, and Quality.
Mitigation: Embrace statistical process control (SPC) methodologies to bring visibility to your processes. Monitor critical parameters, visualize trends, and establish control limits. This proactive approach will highlight process drifts before they lead to major production disruptions.
7Ineffective Troubleshooting:
Root cause analysis becomes a guessing game, marked by repeated breakdowns or recurring quality defects. Without pinpointing the true source of the problem, band-aid fixes lead to a downward spiral of diminishing equipment availability and unreliable output.
Mitigation: Train operators in basic troubleshooting techniques and promote a culture of structured problem-solving. Provide tools like cause-and-effect (fishbone) diagrams or fault tree analysis to guide investigations. Emphasize logging detailed data on downtime incidents, which can reveal patterns over time.
8Wasted Startup Time:
After every shift, changeover, or unplanned stop, production restarts can be chaotic. Inconsistent procedures and a lack of quality checks at startup can lead to extended periods of slow output or outright scrap, eating into your Performance and Quality metrics.
Mitigation: Develop standardized startup checklists and clear quality control protocols for the initial production run. Operators should be trained on these procedures to ensure consistency and quick identification of any deviations from the desired output immediately upon restart.
9Inaccurate Cycle Time Expectations:
Production planning uses theoretical cycle times instead of real-world data. This leads to underestimation of true job durations, overbooking of machines, and a cascade of downstream scheduling problems, eroding both Availability and Performance.
Mitigation: Collect granular machine cycle time data directly from your shop floor. Factor in realistic allowances for minor stoppages, process variability, and operator breaks. Regularly review this data against actual performance to refine your planning processes.
10Unoptimized Batch Sizes:
Sticking with rigid batch sizes without considering product mix or equipment flexibility leads to production inefficiencies. Either you have extended changeover sequences (hurting Availability), or you end up with excess inventory and wasted working capital, affecting Quality down the line.
Mitigation: Move towards a more flexible, demand-driven approach to batch sizing. Analyze customer order patterns, inventory costs, and setup times to identify opportunities for smaller, more frequent production runs. This can boost responsiveness to market needs and reduces the risk of obsolete inventory.
Conclusion: The Path to Data-Driven OEE Excellence Starts Here
By recognizing the telltale signs of “flying blind,” you’ve already taken a crucial step towards maximizing your manufacturing efficiency. The journey to OEE mastery isn’t always easy, but the rewards are undeniable: greater output, reduced costs, and improved customer satisfaction.
Remember, you don’t have to navigate this path alone.
How POWERS Can Help
At POWERS, we’ve dedicated ourselves to helping manufacturers unlock their true OEE potential. Our industry-leading solutions offer:
- Real-time OEE Monitoring: Get instant visibility into your machine performance, revealing hidden losses and guiding data-driven decisions.
- Detailed Root Cause Analysis: Drill down into the heart of your production issues, identifying the factors truly impacting your Availability, Performance, and Quality.
- Customized Improvement Strategies: We work with you to develop targeted action plans and best practices that yield lasting gains.
The journey to manufacturing excellence begins by transforming guesswork into actionable insights. By recognizing the symptoms of “flying blind,” you’re already laying the groundwork for transformative change.
Don’t settle for an OEE that fails to reflect your true potential. Optimize your manufacturing processes and achieve unprecedented efficiency. Contact POWERS today to learn how our expertise can drive your company’s success. Let’s start the conversation by calling us at +1 678-971-4711, emailing us at info@thepowerscompany.com, or filling out our contact form to request an assessment.
- Call: +1 678-971-4711
- Email: info@thepowerscompany.com
- Form: Request Assesment
Don’t wait. Start your journey to operational excellence and achieve peak overall equipment effectiveness with POWERS.
Continue Reading from this Mastery Series
- Part 1 – The Hidden Costs Undermining Your OEE Score
- Part 2 - Dig Deep to Eliminate Inefficiencies that Silently Sabotage Your OEE
- Part 3 – How Guesswork Kills OEE
- Part 4 – When Nobody Takes Ownership OEE Suffers
- Part 5 – When “Pushing Production” Costs You OEE Points
- Part 6 – The Customer Connection: When Dissatisfaction Drains Your OEE
- Part 7 – Death by a Thousand Cuts: How Wear and Tear Steals From Your OEE
- Part 8 – Competitive Disadvantage: The Hidden Enemy of OEE Excellence
- Part 9 – How Missed Opportunities for Improvement Means Missed OEE Potential
- Part 10 – Is Stagnant Innovation Stagnating Your OEE Results