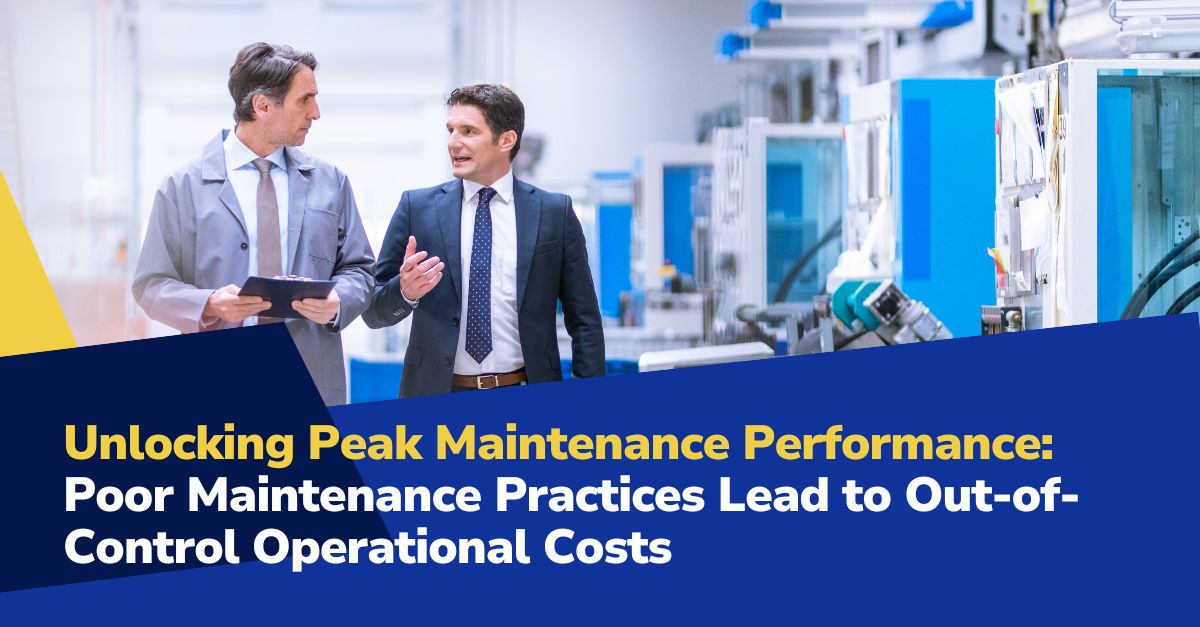
Poor maintenance doesn’t just lead to breakdowns, it quietly drives up operational costs across your facility. From overtime labor to unplanned downtime and inefficient equipment, the cost creep is real, and it adds up fast.
In this sixth installment of our Unlocking Peak Manufacturing Maintenance Performance series, we break down the top 10 ways that inconsistent or reactive maintenance practices drain resources and reduce profitability, and how proactive planning through POWERS’ Advanced Maintenance Performance (AMP) framework helps reverse the damage.
1Emergency Repairs and Off-Hours Work:
When breakdowns happen without warning, teams scramble to respond. That often means bringing in technicians after hours, paying premium rates, and rushing parts deliveries to avoid extended downtime. These unplanned expenses can be double or triple the cost of routine maintenance, and they rarely solve the root cause. Over time, emergency fixes become an expensive habit instead of a rare exception.
2Unplanned Downtime:
The true cost of downtime isn’t just lost production; it’s also idle labor, delayed shipments, and overnight changes to scheduling. Every unplanned stoppage forces a cascade of reactive decisions, from expediting logistics to paying overtime just to stay on track. For many manufacturers, downtime can cost thousands of dollars per hour. When maintenance practices aren’t designed to prevent it, profitability takes a direct hit.
3Increased Equipment Wear and Tear:
Skipping inspections or delaying preventive tasks shortens the life of your assets. Parts run hotter, lubricants degrade, and small issues become mechanical failures. This accelerates depreciation and increases the frequency and severity of repairs, often requiring capital replacement years earlier than expected. These costs rarely appear in budget forecasts, but they land hard when equipment reaches a breaking point.
4Reduced Equipment Efficiency:
Poor maintenance quietly reduces machine performance. Motors work harder, cycles take longer, and energy usage rises. Over time, even a slight drop in efficiency adds up to higher utility costs, more waste, and lower output per labor hour. Well-maintained equipment doesn’t just run longer it runs smarter, supporting productivity targets without unnecessary overhead.
5Quality Control Issues:
Equipment that’s out of spec often creates parts that are out of spec, too. Poor maintenance introduces variability into the process, leading to quality escapes, rejected lots, and costly rework. The impact goes beyond waste it erodes customer trust and forces additional layers of inspection or manual adjustment, all of which slow down throughput and raise cost per unit.
6Safety Hazards and Compliance Risks:
Deferred maintenance creates risk not just to equipment, but to people. Faulty guards, worn wiring, hydraulic leaks, and unstable systems all increase the likelihood of injury. These issues open the door to regulatory fines, rising insurance premiums, and reputational damage. Worse, the true cost of a safety incident is often measured in lost time and long-term disruption not just in paperwork.
7Extended Lead Times:
When key machines are unreliable, production schedules become unpredictable. This forces managers to build in buffer time or rely on backup processes, extending lead times and reducing agility. Customers notice. So do procurement teams and supply chain partners. In competitive markets, long lead times cost business and poor maintenance is often the hidden reason behind the delay.
8Inventory Imbalances:
Reactive maintenance makes it harder to plan production accurately. One day you’re behind, the next day you’re producing just to stay busy. This creates bloated inventories of finished goods you can’t ship, or shortages of high-demand items that customers are waiting on. The result is more storage costs, more write-offs, and less responsiveness to real-time demand.
9Increased Administrative Burden:
When equipment fails frequently, the operations team spends more time chasing fixes than executing strategy. Scheduling repairs, fielding customer complaints, rescheduling deliveries, and tracking root causes becomes a full-time job. This added complexity clogs up workflows and pulls skilled leaders away from forward-looking priorities like productivity planning or process improvement.
10Long-Term Asset Degradation:
Every maintenance shortcut today sets up a bigger cost tomorrow. Equipment that’s consistently run hard and fixed late doesn’t bounce back it wears down. Eventually, it reaches the point where it no longer performs as designed, even with new parts. Replacing assets ahead of schedule ties up capital that could have been invested in growth, technology, or labor development.
How POWERS Helps You Regain Control
At POWERS, we see maintenance as a strategic lever, not just a support function. Our Advanced Maintenance Performance (AMP) and DPS program helps manufacturers build a data-driven, accountable maintenance structure that reduces cost and risk while improving throughput and equipment lifespan.
Rather than relying on emergency fixes or outdated checklists, we help leadership teams:
- Analyze failure patterns and downtime drivers
- Align PM schedules with production realities
- Train teams to recognize early warning signs
- Create escalation paths that reduce response times
- Prioritize repairs that deliver the highest ROI
AMP isn’t just about fixing what’s broken. It’s about preventing failure in the first place and building a maintenance system that supports your long-term profitability.
Conclusions for Senior Operations Leaders
Effective maintenance is a pivotal factor in controlling operational costs and ensuring the longevity and success of manufacturing operations.
By adopting robust and strategic maintenance practices, manufacturers can sidestep the steep costs associated with poor maintenance, paving the way for sustainable growth and enhanced profitability.
For a detailed consultation on improving your manufacturing maintenance practices and reducing operational costs, contact the POWERS team at +1 678-971-4711 or info@thepowerscompany.com.
Continue Reading from this Mastery Series
- Part 1 - The Critical Link Between Maintenance and OEE
- Part 2 - How Maintenance Practices Shape Product Quality
- Part 3 - How Poor Maintenance Standards and Practices Impact Schedule Adherence
- Part 4 - How Maintenance Practices Echo Along the Supply Chain
- Part 5 - The Impact of Maintenance on Maximizing Return on Assets (ROA) in Manufacturing
- Part 6 - Poor Maintenance Practices Lead to Out-of-Control Operational Costs
- Part 7 - Navigating the Safety and Compliance Minefield in Manufacturing
- Part 8 - The High Cost of Overlooking Maintenance in Manufacturing Strategic Planning
- Part 9 - Poor Maintenance Practices Are a Hindrance to Technological Innovations
- Part 10 - Overcoming the ‘Reactive’ or ‘Run Till it Breaks’ Pitfall