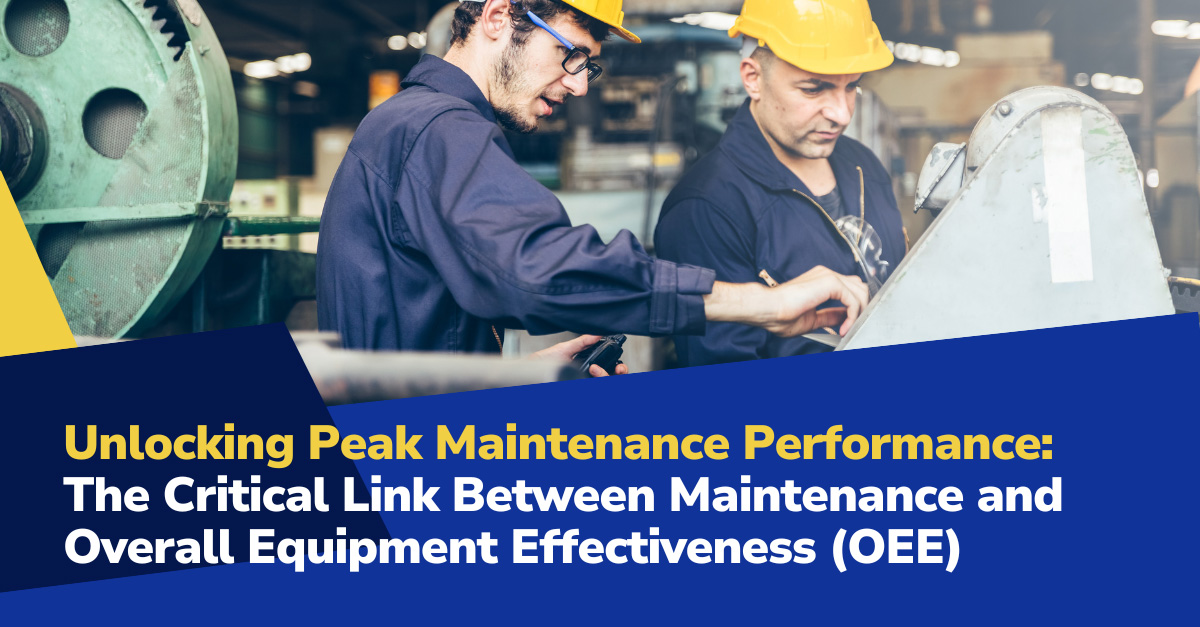
In manufacturing, Overall Equipment Effectiveness (OEE) is one of the clearest indicators of how well your operation is performing. It combines three essential factors, availability, performance, and quality, into a single, measurable score.
High OEE means your machines are running when they should, at the speed they should, producing good parts. But that only happens when your maintenance program is dialed in. When it isn’t, equipment problems don’t just disrupt production, they quietly drag down your entire operation.
This post explores how common maintenance shortcomings erode each pillar of OEE and identifies the top 10 ways they lead to hidden cost, downtime, and performance loss.
AvailabilityThe Foundation of Operational Stability
Availability measures how much planned production time is actually productive. The standard benchmark is around 90%, but when breakdowns become the norm instead of the exception, that number drops fast.
Neglected maintenance leads to unplanned downtime, from sudden mechanical failures to small issues that escalate due to delayed attention. These aren’t just technical issues, they create scheduling headaches, missed orders, and inefficient labor usage. When machines go down without warning, your team shifts from proactive planning to firefighting mode.
Even minor stoppages add up: a few minutes lost per shift over a month can cost hundreds of hours of production.
PerformanceYour Hidden Capacity Loss
Performance evaluates how fast a machine runs compared to its designed capacity. You might hit your production quotas, but if your equipment is running slower than it could, you’re leaving output on the table.
This drop in speed is often gradual and hard to notice. Worn belts, dirty sensors, or poorly lubricated components slow machines down subtly. These hidden slowdowns can reduce performance by 10–20%, quietly undermining your ability to respond to surges in demand or deliver on time without overtime.
Worse, poor performance often forces teams to compensate in the wrong ways, rushing changeovers, skipping quality checks, or pushing past safe operating limits.
QualityThe Cost of Avoidable Mistakes
The quality metric measures how many good units you produce without rework or scrap. A solid operation aims for a 99% quality rate, but even small dips in this number can drain resources fast.
Lack of preventive maintenance leads to misaligned tooling, inconsistent pressure or temperature, and failing sensors, all of which drive up defect rates. These defects don’t just cost you materials, they cost time, trust, and margin.
Quality issues are often the final symptom of deeper maintenance gaps. If you’re constantly adjusting machines between batches or dealing with repeat issues, there’s likely a root cause in your maintenance process.
10 Ways Maintenance Failures Erode OEE (and Profit)
These are the most common maintenance gaps we see in the field, each one a silent threat to your uptime, output, and product quality.
1Increased Equipment Failure Rates:
When preventive tasks are skipped or rushed, breakdowns become more frequent, and more expensive. Studies show poor maintenance can increase failure rates by up to 10x, leading to significant dips in availability and an increase in unplanned repair hours. Frequent failures also burn out your maintenance team, compounding the issue.
2Decline in Cycle Times:
When preventive tasks are skipped or rushed, breakdowns become more frequent, and more expensive. Studies show poor maintenance can increase failure rates by up to 10x, leading to significant dips in availability and an increase in unplanned repair hours. Frequent failures also burn out your maintenance team, compounding the issue.
3Amplified Defect Rates:
As equipment wears or drifts out of spec, quality takes a hit. Defects can climb from 2% to 4% or more, cutting into OEE and increasing your reliance on inspection and rework. Over time, recurring quality issues can damage customer relationships and trigger warranty claims or returns.
4Shortened Machinery Life:
Skipping routine upkeep takes a toll. We’ve seen clients cut their equipment’s expected lifespan by 30–50% due to maintenance neglect. That means reinvesting in capital equipment years earlier than planned, while still dealing with the consequences of poor reliability.
5Surging Maintenance Expenditures:
Emergency repairs, last-minute part orders, and overtime labor can drive reactive maintenance costs to 3–5 times the cost of proactive strategies. These surprises don’t just strain your maintenance budget, they ripple through operations and finance alike.
6Elevated Safety Incidents:
Equipment in poor condition is more likely to cause injuries. Maintenance-related safety incidents can rise 10–20%, often due to failing guards, hydraulic leaks, or mechanical surprises. The fallout, injury reports, lost time, OSHA involvement, brings both financial and reputational damage.
7Increased Energy Consumption:
When machines are out of tune, they work harder and consume more power. Poorly maintained equipment can draw 10–30% more energy, quietly inflating your utility bills and carbon footprint. It’s a cost few companies track, but one that adds up quickly across multiple lines or shifts.
8Variability in Production:
Inconsistent equipment performance leads to inconsistent outputs. That unpredictability can skew forecasts, disrupt planning, and force inefficient buffer stocks. We’ve seen variability increase by 25% or more in plants with no maintenance standardization.
9Gap in Maintenance Skills:
Even with the right tools, poor training leaves your team guessing. A 20–40% skills gap in core maintenance practices can slow down repairs, increase error rates, and make your most reliable machines vulnerable to operator misuse or overcorrection.
10Maintenance Process Inefficiencies:
Too many plants still rely on paper logs, reactive scheduling, or outdated CMMS setups. This extends repair times by up to 50%, especially when parts aren’t staged, priorities aren’t clear, or handoffs between shifts break down.
The POWERS Difference
Recognizing these metrics and the profound effects they have on OEE, the Manufacturing Productivity Experts at POWERS have engineered the AMP (Advanced Maintenance Performance) program. This comprehensive solution not only assesses the current state of your maintenance but also provides a strategic blueprint for improvement, ensuring that each component of OEE is optimized for peak performance.
Embark on a transformative journey toward maintenance excellence. Explore the POWERS difference with a thorough OEE analysis, skill and training enhancements, and a robust, actionable plan for implementation. Elevate your maintenance team and overall performance to new heights.
To gain a deeper understanding and take the first step towards optimized maintenance, download our FREE Maintenance Assessment Guide. Begin your optimization journey by contacting the POWERS team at +1 678-971-4711 or via email at info@thepowerscompany.com.
Continue Reading from this Mastery Series
- Part 1 - The Critical Link Between Maintenance and OEE
- Part 2 - How Maintenance Practices Shape Product Quality
- Part 3 - How Poor Maintenance Standards and Practices Impact Schedule Adherence
- Part 4 - How Maintenance Practices Echo Along the Supply Chain
- Part 5 - The Impact of Maintenance on Maximizing Return on Assets (ROA) in Manufacturing
- Part 6 - Poor Maintenance Practices Lead to Out-of-Control Operational Costs
- Part 7 - Navigating the Safety and Compliance Minefield in Manufacturing
- Part 8 - The High Cost of Overlooking Maintenance in Manufacturing Strategic Planning
- Part 9 - Poor Maintenance Practices Are a Hindrance to Technological Innovations
- Part 10 - Overcoming the ‘Reactive’ or ‘Run Till it Breaks’ Pitfall