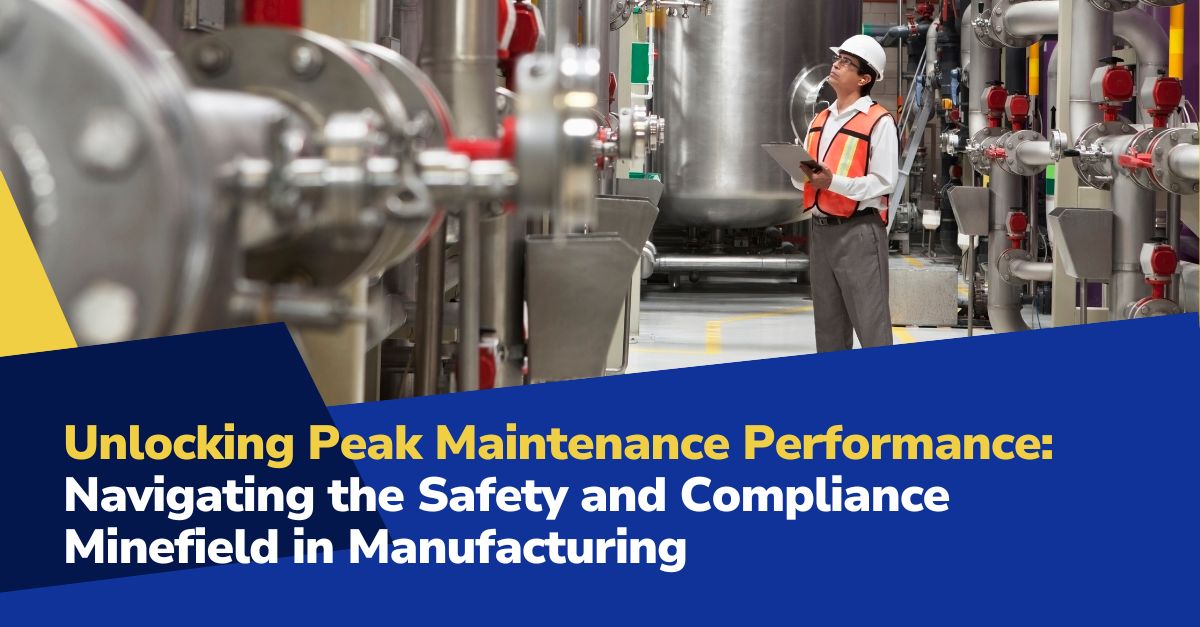
Maintenance in manufacturing isn’t just about preventing breakdowns, it’s about protecting people, meeting regulations, and safeguarding your company’s future. When maintenance falls short, the consequences ripple across operations, from avoidable injuries to regulatory penalties and damaged customer relationships.
In this installment, we explore 10 critical ways poor maintenance practices undermine safety and compliance and how these risks quietly drive up costs that can erode profitability over time.
1Elevated Accident Risks:
When equipment isn’t properly maintained, it becomes unpredictable and dangerous. Faulty machinery contributes to roughly 1 in 10 workplace injuries in manufacturing, often leading to serious incidents like crush injuries, electrical shocks, or fires. These accidents don’t just generate direct costs such as emergency medical care they can trigger investigations, long-term disability claims, and increased oversight by regulators. Even a single incident can remove skilled employees from the floor for months, create production delays, and force other team members to pick up extra shifts.
2Regulatory Fines and Sanctions:
Regulatory agencies like OSHA and state safety boards hold manufacturers to clear standards. Missed inspections, ignored repairs, incomplete lockout/tagout procedures, or missing documentation can all lead to citations. Fines regularly exceed $100,000 per violation, especially if inspectors find a pattern of neglect or repeat offenses. In some cases, regulators can temporarily shut down operations or impose costly abatement measures that divert capital away from growth and improvement initiatives. Over time, these violations stay on record, which can impact your reputation with customers, investors, and insurers.
3Increased Insurance Premiums:
Insurance carriers look closely at maintenance records and claims history when calculating risk. A pattern of equipment-related accidents or safety failures often results in higher premiums and deductibles that continue year after year. In some cases, insurers may even require proof of corrective actions and maintenance upgrades before renewing coverage. Over time, these added costs can quietly drain cash flow and make it harder to reinvest in technology, facilities, and workforce development.
4Downtime Due to Safety Incidents:
When an incident occurs, production lines can grind to a halt with little warning. Unplanned shutdowns often last longer than expected, as internal investigations, insurance assessments, and regulatory reviews unfold. Specialized machinery may need to be inspected, repaired, or recalibrated before operations resume safely. Each hour of downtime compounds losses idle labor, delayed shipments, overtime to catch up, and frustrated customers whose orders are late. For many manufacturers, these hidden costs can exceed the price of proactively maintaining equipment.
5Legal Liabilities and Litigation Costs:
When an injury or fatality happens due to neglected maintenance, legal action is often inevitable. Lawsuits over unsafe working conditions, negligence, or regulatory violations can lead to settlements or judgments that stretch into millions of dollars. Even if claims are settled out of court, the time and resources consumed by litigation are significant. Publicly disclosed cases can also damage hard-won relationships with customers and suppliers, while internal morale suffers under the stress of ongoing legal battles.
6Compromised Worker Morale and Productivity:
No one wants to work with equipment they don’t trust. When employees feel unsafe, morale declines and productivity suffers. Workers may hesitate to operate machinery, slow down production to double-check processes, or spend extra time documenting concerns. Over time, this environment increases the chance of errors, reduces efficiency, and drives higher turnover. Replacing experienced staff is expensive and time-consuming, requiring additional recruitment and training that further strains resources.
7Loss of Reputation:
In today’s digital world, news about safety failures spreads quickly sometimes within hours. Headlines about preventable injuries, fires, or environmental incidents can seriously damage your brand and erode trust with customers, partners, and the community. Companies often face years of rebuilding their reputation and investing in public relations campaigns to restore confidence. In some industries, a single high-profile incident can jeopardize long-term contracts or trigger customer audits that disrupt operations.
8Training and Retraining Costs:
After a safety incident, most companies must pause to retrain employees on safety procedures, maintenance protocols, and regulatory requirements. These unplanned sessions pull people off the production floor, create scheduling headaches, and reduce throughput. The costs quickly add up hiring external trainers, updating materials, and dedicating staff hours to compliance instead of production. Frequent retraining due to repeated maintenance failures signals deeper issues and often leads to higher turnover as employees grow frustrated.
9Environmental Hazards:
Poor maintenance doesn’t just impact people it can also harm the environment. Leaking pipes, corroded tanks, or faulty containment systems can cause chemical spills, fires, or air quality violations. Environmental incidents often trigger cleanup costs, regulatory penalties, and lawsuits from local communities or environmental groups. For manufacturers handling hazardous materials, these events can have long-term consequences, including tighter scrutiny, higher insurance premiums, and lasting reputational harm.
10Resource Drain on Safety Monitoring and Compliance:
When maintenance is reactive rather than proactive, companies must dedicate extra resources to safety monitoring, audits, and reporting to stay compliant. These efforts pull time and budget away from other priorities like process improvement, capacity expansion, and innovation. Over time, the constant scramble to fix problems as they arise creates a culture of firefighting that drains leadership focus and wears down teams.
The POWERS Difference:
Safeguarding Through Maintenance Excellence
At POWERS, we understand that reliable maintenance is the foundation of a safe, compliant, and efficient operation. Too often, manufacturers end up stuck in a reactive cycle fixing problems after they cause injuries, shutdowns, or regulatory trouble.
That’s why we built our Advanced Maintenance Performance (AMP) program to help you move from crisis management to proactive excellence.
Here’s what our approach delivers:
- Clear Processes and Standards: We work side by side with your teams to establish consistent maintenance protocols, inspection routines, and documentation practices so nothing falls through the cracks.
- Data-Driven Insights: Using our proprietary frameworks, we help you track and analyze maintenance performance to spot patterns early before small issues become major safety risks.
- Skills Development and Training: We provide practical coaching for supervisors and frontline staff, ensuring everyone knows how to maintain equipment safely and stay compliant with regulations.
By implementing AMP, manufacturers can:
- Reduce accidents and injuries that disrupt operations
- Achieve and sustain compliance with OSHA and other regulatory standards
- Lower insurance costs and legal exposure
- Protect your brand reputation and customer confidence
- Improve employee engagement and retention by creating a safer workplace
In addition, our Digital Production System (DPS), offers robust digital tools that complement AMP by digitizing maintenance schedules, automating compliance reporting, and providing real-time visibility into asset performance. Together, POWERS and DPS help you build a maintenance program that’s not only reliable but also modern, measurable, and easier to manage.
Are you ready to transform your maintenance practices into a bulwark of safety and compliance? Contact our dedicated team at +1 678-971-4711 or info@thepowerscompany.com for a comprehensive assessment and tailored solutions.
Let’s build a safer, more compliant, cost-effective manufacturing environment.
Continue Reading from this Mastery Series
- Part 1 - The Critical Link Between Maintenance and OEE
- Part 2 - How Maintenance Practices Shape Product Quality
- Part 3 - How Poor Maintenance Standards and Practices Impact Schedule Adherence
- Part 4 - How Maintenance Practices Echo Along the Supply Chain
- Part 5 - The Impact of Maintenance on Maximizing Return on Assets (ROA) in Manufacturing
- Part 6 - Poor Maintenance Practices Lead to Out-of-Control Operational Costs
- Part 7 - Navigating the Safety and Compliance Minefield in Manufacturing
- Part 8 - The High Cost of Overlooking Maintenance in Manufacturing Strategic Planning
- Part 9 - Poor Maintenance Practices Are a Hindrance to Technological Innovations
- Part 10 - Overcoming the ‘Reactive’ or ‘Run Till it Breaks’ Pitfall