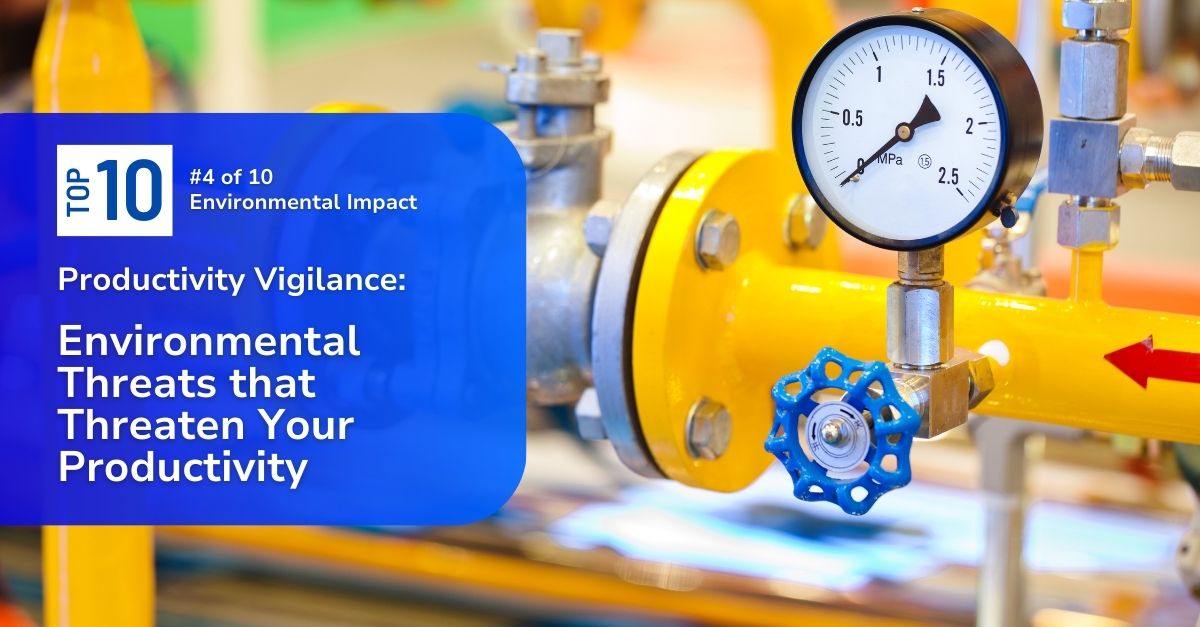
You might think environmental concerns are the domain of regulatory compliance or public relations – something outside the immediate responsibilities of a production manager.
However, the ripple effects of climate change, pollution, and resource scarcity have a very real and significant impact on the efficiency of your manufacturing operations.
Imagine a heatwave strains your local power grid, causing unpredictable rolling brownouts. Production lines shut down abruptly, sensitive materials may be ruined, and equipment suffers potential damage. The impacts are immediate, but the hidden losses continue:
- Increased maintenance time is needed to restart and recalibrate machinery.
- Production schedules become chaotic as you try to compensate for lost time.
- Customer orders might be delayed, eroding trust and creating backlogs.
The initial power outage is the environmental trigger, but productivity suffers from those secondary and often less obvious consequences.
This blog post highlights the top 10 ways environmental impact undermines manufacturing productivity. More importantly, it provides actionable mitigation strategies to empower you to build a more resilient and sustainable operation.
1Product Recalls Due to Unexpected Contamination Discovered Post-Production:
Product recalls are highly disruptive to manufacturing productivity. They halt production lines, divert resources toward investigating the source of contamination, necessitate reworking or scrapping inventory, and damage customer trust. This translates to significant delays in production schedules, lost revenue, and increased operational costs, severely hindering overall productivity.
Mitigation: Establishing a comprehensive Environmental Management System (EMS) with stringent quality control protocols is paramount. Regular testing of raw materials, in-process materials, and finished products can identify potential contamination early on, allowing for immediate corrective action before it escalates into a full-scale recall. Implementing robust traceability systems can also help pinpoint the source of contamination quickly, minimizing the scope of the recall and its impact on productivity.
2Specialized Cleaning Procedures to Meet Environmental Standards:
While necessary for compliance, specialized cleaning procedures often involve additional time, labor, and specialized equipment. This can significantly slow down production cycles, extend lead times, and increase labor costs. These procedures can also necessitate temporary shutdowns or reduced production rates, further impacting productivity.
Mitigation: Investing in efficient, effective, and compliant, eco-friendly cleaning technologies can reduce the time and resources required for cleaning. Automating cleaning processes can further minimize disruption to production schedules, as automated systems can operate during off-hours or alongside production without requiring manual labor.
3Damage to Machinery from Corrosive Pollutants:
Corrosive pollutants in the manufacturing environment can lead to accelerated wear and tear on machinery, leading to unexpected breakdowns, costly repairs, and unplanned downtime. These disruptions can significantly reduce production output, increase maintenance expenses, and disrupt production schedules, ultimately hindering productivity.
Mitigation: Implementing a proactive maintenance program that includes regular inspections, cleaning, and lubrication can help mitigate the effects of corrosion. Applying protective coatings to machinery surfaces can also shield them from corrosive elements. Additionally, investing in air filtration systems can help remove corrosive pollutants from the air, further protecting equipment and ensuring smooth production flow.
4Water Contamination Events Leading to Material Quality Issues:
Water contamination events can have a cascading effect on manufacturing productivity. Contaminated water used in production processes can lead to defects in finished products, increased scrap rates, and customer returns. This results in the need for costly rework, production delays, and potential damage to brand reputation, all of which negatively impact overall productivity.
Mitigation: Robust water treatment and purification systems are essential to ensure the quality of water used in manufacturing processes. Regular testing and monitoring of water sources can help identify contamination early, allowing for swift corrective action before it impacts product quality. Implementing redundant water supply systems can also provide backup in the event of contamination.
5Storage Limitations Due to Strict Regulations for Hazardous Materials:
Regulations governing the storage of hazardous materials often impose limits on storage capacity. This can create bottlenecks in the production process, as manufacturers may not be able to store sufficient quantities of raw materials or finished goods, leading to production delays and lost opportunities.
Mitigation: Optimizing inventory management practices, such as just-in-time (JIT) delivery and demand forecasting, can help manufacturers operate efficiently within the constraints of limited storage capacity. Evaluating the use of alternative, less hazardous materials can also reduce the need for specialized storage facilities, freeing up valuable space and streamlining production processes.
6Need to Redesign Products to Reduce Environmental Impact:
Redesigning products to meet evolving environmental standards can be a complex and time-consuming process that requires significant investment in research and development (R&D). This can delay product launches, disrupt established production lines, and strain resources, ultimately impacting productivity.
Mitigation: Integrating eco-design principles early in the product development process can help avoid costly redesigns later. This involves considering the product’s entire lifecycle, from raw material sourcing to disposal. Partnering with suppliers who offer sustainable materials and utilizing life cycle assessment (LCA) tools can further streamline the redesign process and minimize its impact on productivity.
7Production Limitations Imposed by Air or Water Quality Permits:
Environmental permits often impose limits on emissions and discharges, which can directly constrain production capacity. To comply with these restrictions, manufacturers may need to reduce output, invest in expensive pollution control technologies, or incur fines for non-compliance. This can lead to reduced productivity and increased operational costs.
Mitigation: Investing in cleaner production technologies can help manufacturers reduce emissions and comply with environmental permits without sacrificing productivity. Implementing energy-efficient equipment and processes can further minimize environmental impact while lowering energy costs, contributing to both environmental and economic sustainability.
8Mandatory Retrofitting of Older Facilities:
Retrofitting older facilities to meet current environmental standards can be a disruptive and costly process. It often involves temporary shutdowns or reduced production rates while upgrades are being implemented. This can lead to production delays, increased labor costs, and potential revenue losses.
Mitigation: Careful planning and phased implementation of retrofits can minimize disruptions to production schedules. Engaging with experienced contractors who specialize in environmental upgrades can also ensure that projects are completed efficiently and on time.
9Elevated Product Rejection Rates Due to Stricter Customer Environmental Standards:
As customer expectations for environmentally friendly products rise, stricter environmental standards can lead to higher product rejection rates. This necessitates rework, disposal, or additional inspections, all of which consume valuable resources and time, ultimately decreasing productivity.
Mitigation: Engaging with customers early in the product development process to understand their specific environmental requirements is crucial. This can help ensure that products are designed to meet or exceed these standards from the outset, minimizing the risk of rejection. Implementing robust quality control processes throughout production can also identify defects early, reducing the need for rework and ensuring that only compliant products reach customers.
10Production Schedule Changes to Avoid Peak Energy Demand Periods:
Shifting production schedules to avoid peak energy demand can disrupt established workflows and require additional labor for off-peak shifts. This can lead to increased labor costs, potential overtime expenses, and challenges in coordinating with suppliers and customers.
Mitigation: Investing in energy storage solutions can be a game-changer. By storing excess energy generated during off-peak hours, manufacturers can maintain consistent production schedules and avoid the productivity losses associated with schedule adjustments. Additionally, exploring demand response programs offered by utility companies can provide financial incentives for shifting energy use to off-peak periods.
Conclusion for Manufacturing Operations Leaders
The environmental challenges facing manufacturing are not going away. In fact, the frequency and intensity of disruptions are likely to increase. The question is not whether your facility will be impacted but how well you’re prepared. Proactive mitigation and adaptation are not just about environmental responsibility; they are crucial for ensuring long-term productivity, profitability, and competitiveness.
How POWERS Can Help
Our team brings not only deep manufacturing expertise but also specializes in Productivity Vigilance – the comprehensive analysis of factors impacting your output and efficiency. We help you:
- Uncover Hidden Vulnerabilities: Conduct a thorough assessment of your facility's exposure to environmental risks, identifying both direct and indirect impacts on productivity.
- Develop Data-Driven Solutions: We utilize operational data and predictive analytics to model potential disruptions and tailor mitigation strategies for maximum impact.
- Prioritize Investments: Create a prioritized roadmap of investments, from equipment upgrades to process optimization, ensuring the greatest productivity gains.
- Speak to an Expert: Call +1 678-971-4711 to discuss your specific challenges and goals.
- Email Us: Get tailored insights by emailing info@thepowerscompany.com
- Request an Assessment: Use our online contact form, and one of our expert manufacturing consultants will reach out to schedule an in-depth analysis of your operations.
Continue Reading from this Mastery Series
- Part 1 – Without Top Talent, Top Productivity is Elusive
- Part 2 – How Blind Spots in Cost Analysis Hide Your Productivity Struggles
- Part 3 – When Supply Chain Issues Deliver A Productivity Hit
- Part 4 – Environmental Threats that Threaten Your Productivity
- Part 5 – Don’t Let Scaling Up Bring Down Your Productivity
- Part 6 – How Vulnerabilities to Disruptions Undermine Productivity
- Part 7 – Why Ignoring TPM Means Missing Out on Productivity Goals
- Part 8 – How Poor Training and Development Creates Productivity Shortfalls
- Part 9 – How Delayed NPIs Lead to Productivity Misses
- Part 10 – How Inaccurate Data Obscures Productivity Insight