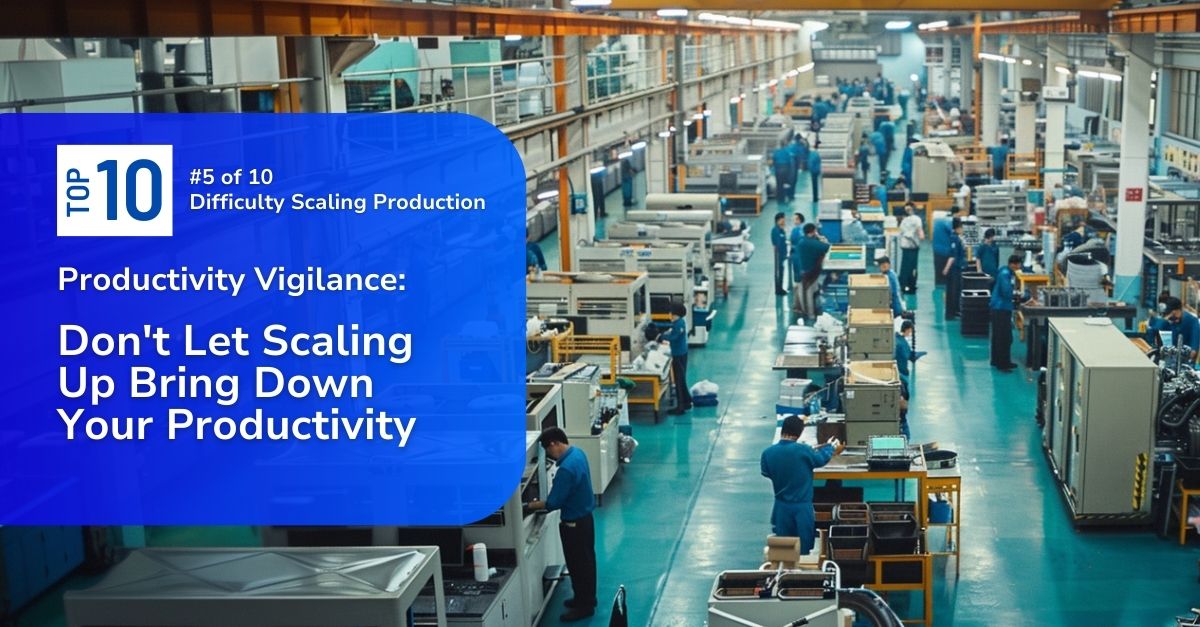
Scaling production is a critical aspect of growth in the manufacturing industry. As demand increases, companies must scale their operations to meet market needs, expand their market share, and maximize profitability.
However, this scaling process often introduces significant challenges that can hinder productivity.
For instance, consider a mid-sized automotive parts manufacturer that recently expanded its production lines to meet a surge in demand. Initially, the company enjoyed increased output and higher revenue. However, as the scaling progressed, the production lines began to experience frequent downtime due to insufficient maintenance personnel. The increased demand for maintenance overwhelmed the existing team, leading to delays in repairs and extended periods of inactivity. This downtime, a secondary symptom of the rapid scaling, significantly reduced overall productivity, causing missed deadlines and strained client relationships.
This post delves into the top 10 ways Difficulty Scaling Production negatively impacts manufacturing productivity. We will explore the secondary symptoms and provide practical mitigation strategies for each issue, ensuring managers can navigate these challenges effectively.
1Increased Downtime Due to Lack of Maintenance Personnel:
As production scales up, the demand for maintenance increases correspondingly. However, a common problem is the shortage of skilled maintenance personnel, which leads to increased equipment downtime. When machines break down, the lack of immediate maintenance resources can halt production lines, leading to significant productivity losses.
Mitigation: To address this issue, manufacturers should invest in cross-training production staff with basic maintenance skills. Additionally, implementing predictive maintenance technologies can help anticipate and prevent equipment failures. By using sensors and data analytics, companies can monitor the health of their machines and schedule maintenance during planned downtimes, minimizing unexpected disruptions.
2Lack of Standardization Leading to Inconsistent Processes:
Scaling production often introduces variability in processes due to the lack of standardization. This inconsistency can lead to quality issues, inefficiencies, and increased waste, ultimately reducing overall productivity. Inconsistent processes also make it challenging to train new employees and maintain a stable production flow.
Mitigation: Establishing standardized operating procedures (SOPs) is crucial for maintaining consistency. Regular audits and updates of these SOPs can ensure they remain relevant and effective. Additionally, investing in comprehensive training programs for employees can reinforce the importance of adhering to standardized processes, thus enhancing productivity.
3Higher Defect Rates Due to Pressure to Increase Output:
The pressure to meet higher production targets can compromise quality control, leading to increased defect rates. When employees are pushed to prioritize quantity over quality, the risk of producing defective products rises. This not only wastes resources but also damages the company’s reputation and customer satisfaction.
Mitigation: Implementing robust quality control systems and fostering a culture that values quality over sheer output is essential. Regular quality audits and encouraging employees to report potential issues without fear of retribution can help maintain high standards. Utilizing Six Sigma methodologies can also reduce defects and improve overall productivity.
4Increased Bureaucracy Due to More Rules and Procedures:
As companies grow, the addition of new rules and procedures can create bureaucratic hurdles that slow down decision-making and operational efficiency. This increased bureaucracy can stifle innovation, delay responses to production issues, and reduce overall productivity.
Mitigation: Streamlining procedures and eliminating unnecessary steps can help reduce bureaucracy. Implementing lean management principles to identify and eliminate waste in processes can also enhance efficiency. Encouraging a culture of continuous improvement where employees can suggest and implement changes can further mitigate the negative impacts of bureaucracy.
5Difficulty in Coordinating and Managing Multiple Production Lines:
Managing multiple production lines introduces complexities in coordination and resource allocation. Without proper management, these complexities can lead to scheduling conflicts, resource shortages, and production delays, all of which negatively impact productivity.
Mitigation: Utilizing advanced production planning and scheduling software can help manage multiple lines more effectively. These tools can optimize resource allocation, synchronize production schedules, and provide real-time visibility into operations. Regular coordination meetings with key stakeholders can also ensure alignment and promptly address any emerging issues.
6Hasty Automation Implementation Leading to Increased Errors:
In the rush to scale production, companies might hastily implement automation without thorough planning and testing. This can result in increased errors, machine malfunctions, and downtime, ultimately reducing productivity instead of enhancing it.
Mitigation: A phased approach to automation, starting with pilot projects and gradual scaling, can help mitigate these issues. Involving experienced automation experts and conducting thorough testing and validation before full-scale implementation can ensure a smoother transition. Continuous monitoring and optimization of automated processes can further enhance productivity.
7Challenges in Managing Inventory Levels Leading to Downtime:
Scaling production often complicates inventory management. Poor inventory control can lead to shortages or overstocking, both of which disrupt production. Inventory shortages can halt production lines while overstocking ties up capital and storage space.
Mitigation: Implementing advanced inventory management systems that use real-time data and predictive analytics can optimize inventory levels. Just-in-time (JIT) inventory practices can also minimize the risk of overstocking while ensuring that materials are available when needed. Regular inventory audits and adjustments based on demand forecasts can further enhance inventory management.
8Less Collaboration Due to Silos from Larger Teams/Shifts:
As production scales and teams grow, silos can form, reducing collaboration and communication. This fragmentation can lead to misaligned goals, redundant efforts, and inefficiencies that negatively affect productivity.
Mitigation: Encouraging cross-functional teams and implementing collaborative tools can break down silos. Regular inter-departmental meetings and team-building activities can foster better communication and collaboration. Adopting a unified communication platform can also ensure that all teams are on the same page, enhancing overall productivity.
9Longer Cycle Times Due to New Bottlenecks or Waiting Times:
Scaling production can introduce new bottlenecks and increase waiting times in the production process, leading to longer cycle times. These delays can slow down the entire production line, reducing throughput and overall productivity.
Mitigation: Conducting thorough process analysis and using tools like Value Stream Mapping (VSM) can help identify and address bottlenecks. Continuous improvement methodologies like Kaizen can be employed to optimize processes and reduce waiting times. Regularly reviewing and adjusting production workflows can ensure smoother and more efficient operations.
10Difficulty in Maintaining Effective Communication Across Departments:
Effective communication becomes more challenging as the scale of production increases and more departments are involved. Miscommunication can lead to errors, delays, and conflicts, all of which negatively impact productivity.
Mitigation: Implementing clear communication protocols and using integrated communication platforms can enhance information flow. Regular training on effective communication and encouraging an open-door policy can also improve inter-departmental communication. Establishing a centralized communication hub where all updates and critical information are shared can further streamline communication and improve productivity.
Overcoming Scaling Challenges for Manufacturing Leadership
In the intricate dance of scaling production, the secondary symptoms we’ve explored can easily become the Achilles’ heel of your manufacturing operation. These subtle productivity killers can quietly erode your gains, leaving you grappling with unexpected setbacks.
But armed with the insights and mitigation strategies outlined in this guide, you’re well-equipped to navigate these treacherous waters. By proactively addressing the challenges of maintenance, standardization, quality control, automation, inventory management, communication, and collaboration, you can transform scaling from a potential pitfall into a springboard for sustained growth.
POWERS: Your Partner in Productivity Vigilance
At POWERS, we understand the unique challenges that manufacturers face when scaling production. Our team of experts is dedicated to helping you identify and address the secondary symptoms that can undermine your productivity.
Through our Productivity Vigilance methodology, we work closely with you to analyze your operations, pinpoint areas of vulnerability, and develop tailored solutions that drive sustainable growth. Whether it’s optimizing maintenance schedules, streamlining communication channels, or implementing cutting-edge automation, we’re committed to empowering you with the tools and strategies you need to thrive in the ever-evolving manufacturing landscape.
Let POWERS be your trusted partner in the journey toward scaling success. Together, we can unlock the full potential of your manufacturing operation, ensuring that growth translates into enhanced productivity, profitability, and resilience.
Contact POWERS today to learn more about how we can help you achieve your manufacturing goals.
- Speak to an Expert: Call +1 678-971-4711 to discuss your specific challenges and goals.
- Email Us: Get tailored insights by emailing info@thepowerscompany.com
- Request an Assessment: Use our online contact form, and one of our expert manufacturing consultants will reach out to schedule an in-depth analysis of your operations.
Continue Reading from this Mastery Series
- Part 1 – Without Top Talent, Top Productivity is Elusive
- Part 2 – How Blind Spots in Cost Analysis Hide Your Productivity Struggles
- Part 3 – When Supply Chain Issues Deliver A Productivity Hit
- Part 4 – Environmental Threats that Threaten Your Productivity
- Part 5 – Don’t Let Scaling Up Bring Down Your Productivity
- Part 6 – How Vulnerabilities to Disruptions Undermine Productivity
- Part 7 – Why Ignoring TPM Means Missing Out on Productivity Goals
- Part 8 – How Poor Training and Development Creates Productivity Shortfalls
- Part 9 – How Delayed NPIs Lead to Productivity Misses
- Part 10 – How Inaccurate Data Obscures Productivity Insight