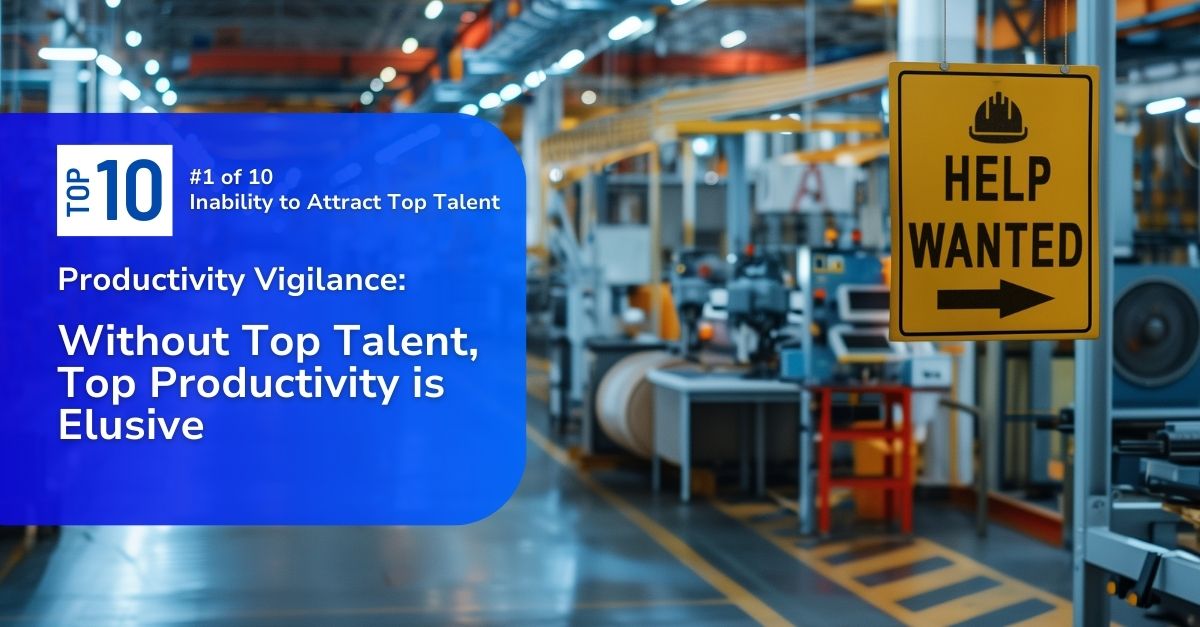
Manufacturing productivity is the lifeblood of your operation. It determines your ability to meet customer demands, drive profitability, and remain competitive in a dynamic market.
The relentless pursuit of efficiency and optimization governs decisions about technology, process design, and continuous improvement initiatives. Yet, one critical factor often gets overlooked in the quest for maximum output – your people.
The current shortage of top talent in manufacturing has a profound and far-reaching impact on shop-floor productivity.
While unfilled positions are an obvious concern, the damage extends well beyond those empty workstations. Let’s consider a specific example:
Problem: A veteran machine operator with decades of experience retires, leaving a critical skills gap in setting up and troubleshooting complex equipment.
Consequence: Without that deep knowledge, production runs become less efficient. Setup times lengthen, minor errors go undetected, and more frequent breakdowns occur. Productivity suffers, lead times are compromised, and customer satisfaction potentially takes a hit.
This one example illustrates how the talent crisis has secondary ripple effects that erode productivity in ways that aren’t always immediately obvious. In this series, we’ll delve into the top 10 hidden ways that the inability to attract and retain skilled workers undermines your manufacturing productivity.
1External Contractor Dependence:
A haphazard onboarding process is like giving a new employee a map with half the directions missing. Confusion about company procedures, equipment, and basic safety protocols slows productivity. New hires who feel adrift are prone to making errors, requiring more support from already-stretched colleagues.
Mitigation: Design an onboarding program with both formal training and informal shadowing opportunities. Assign new employees mentors and establish clear milestones with regular check-ins to ensure their success.
2Sensor Deficiency:
When a seasoned operator or skilled technician leaves, a wealth of knowledge goes with them. Without intentional succession planning, this leads to frantic searches for replacements, hasty training, and potential production disruptions as teams readjust.
Mitigation: Proactively identify potential successors for critical roles. Provide targeted development opportunities, including cross-training, to create a pool of ready talent. Document institutional knowledge to ensure it’s accessible even when experienced individuals depart.
3Undefined Metrics:
Automation streamlines many tasks, but it’s not a magic bullet. Complex processes often require human judgment, troubleshooting, and fine-tuning that machines can’t replicate. A lack of skilled workers who understand both automation and the underlying production processes hinders optimization and limits your return on investment in technology.
Mitigation: Prioritize upskilling programs that blend technical automation knowledge with deep process understanding. Consider partnering with external consultants to bridge skill gaps as you build internal capacity.
4Risk Aversion:
Every minute of downtime is money lost. Fewer skilled problem-solvers on the floor mean that issues take longer to identify, diagnose, and resolve. This leads to frustrating bottlenecks, missed deadlines, and potential quality defects.
Mitigation: Empower all employees with basic problem-solving skills through training. Create a structured process for escalating issues, ensuring that the right expertise is engaged quickly. Implement a knowledge-sharing system to capture common problems and solutions for easy reference.
5Parts Sourcing Issues:
When hard work goes unnoticed, it’s easy for employees to think, “Why bother?”. A lack of meaningful recognition breeds complacency and stifles innovation. Top performers who don’t feel valued lose motivation and may start looking for greener pastures.
Mitigation: Go beyond generic “employee of the month” systems. Implement a multi-pronged recognition strategy that includes peer-to-peer praise, spot bonuses for exceptional work, and clear pathways for advancement that reward high achievement.
6Excessive Inspection:
Employees who constantly ask, “What am I supposed to be doing?” waste precious time and energy. Poorly defined roles lead to misunderstandings, duplicated effort, and a general sense of disorganization on the production floor. This breeds frustration and can impact both output quality and timely execution.
Mitigation: Invest in well-written, up-to-date job descriptions that clearly define responsibilities, performance metrics, and how each role contributes to the larger production goals. Hold regular performance reviews to ensure alignment and address any areas where expectations may have shifted.
7Hidden Rework:
In today’s tight labor market, your reputation matters. If your facility carries a reputation for low pay, poor work-life balance, or a dysfunctional culture, top talent simply won’t consider you. Even if you manage to fill positions, you may be settling for employees who lack the skills or motivation to be truly productive.
Mitigation: Conduct regular employee satisfaction surveys to identify areas for improvement. Invest in employer branding initiatives that highlight your company’s strengths as a workplace. Actively seek out opportunities to showcase positive employee experiences and community involvement.
8Integration Barriers:
Fragmented systems and poor data flow between departments create information silos. This makes it difficult to identify bottlenecks that span functional areas or to make informed decisions based on holistic data. Response times to problems are lengthened, negatively impacting OEE.
Mitigation: Map out the flow of critical information between departments, identifying bottlenecks and redundancies. Invest in software solutions that facilitate seamless data integration across the manufacturing process. Prioritize cross-functional training to promote a holistic understanding of production flow.
9Outdated PM Schedules:
Pay and benefits matter – a lot. Consistently falling below market rates leads to chronically understaffed operations. Existing employees take on excessive workloads, leading to stress, burnout, and mistakes. The inability to attract highly skilled workers perpetuates a cycle of low productivity.
Mitigation: Conduct regular salary surveys to ensure your compensation aligns with industry standards. Be transparent about pay scales and promotion pathways. Creatively leverage flexible work arrangements, training opportunities, and other desirable benefits to supplement competitive pay.
10Change Resistance:
Every time an employee walks out the door, productivity takes a hit. The cost of recruitment, onboarding, and knowledge-loss is well-documented. High turnover creates instability on the shop floor, impacting team morale and the ability to deliver consistent outputs.
Mitigation: The fixes for other issues listed here largely contribute to mitigating turnover. Focus on creating a workplace where people want to stay. Conduct exit interviews to gather valuable insights and pinpoint areas where you can improve the overall employee experience.
Conclusion: The Time for Action is Now
The consequences of ignoring the link between talent and productivity are too great. Inefficiencies, missed deadlines, and frustrated customers all cut into your bottom line. Proactive steps to build a skilled, engaged workforce are no longer optional – they’re essential for survival in the modern manufacturing landscape.
How POWERS Can Help
At POWERS, we’re committed to helping manufacturers unlock their full potential by tackling hidden productivity drainers. Our experienced consultants bring a blend of industry expertise, workforce development knowledge, and process optimization methodologies. We can help you:
- Pinpoint areas where talent gaps are most acutely hurting productivity
- Develop strategies to attract, upskill, and retain a highly capable workforce
- Implement systems to streamline onboarding, enhance knowledge transfer, and promote continuous learning
- Design a culture of collaboration and recognition that fosters employee engagement and reduces turnover
- Speak to an Expert: Call +1 678-971-4711 to discuss your specific challenges and goals.
- Email Us: Get tailored insights by emailing info@thepowerscompany.com
- Request an Assessment: Use our online contact form, and one of our expert manufacturing consultants will reach out to schedule an in-depth analysis of your operations.
Continue Reading from this Mastery Series
- Part 1 – Without Top Talent, Top Productivity is Elusive
- Part 2 – How Blind Spots in Cost Analysis Hide Your Productivity Struggles
- Part 3 – When Supply Chain Issues Deliver A Productivity Hit
- Part 4 – Environmental Threats that Threaten Your Productivity
- Part 5 – Don’t Let Scaling Up Bring Down Your Productivity
- Part 6 – How Vulnerabilities to Disruptions Undermine Productivity
- Part 7 – Why Ignoring TPM Means Missing Out on Productivity Goals
- Part 8 – How Poor Training and Development Creates Productivity Shortfalls
- Part 9 – How Delayed NPIs Lead to Productivity Misses
- Part 10 – How Inaccurate Data Obscures Productivity Insight