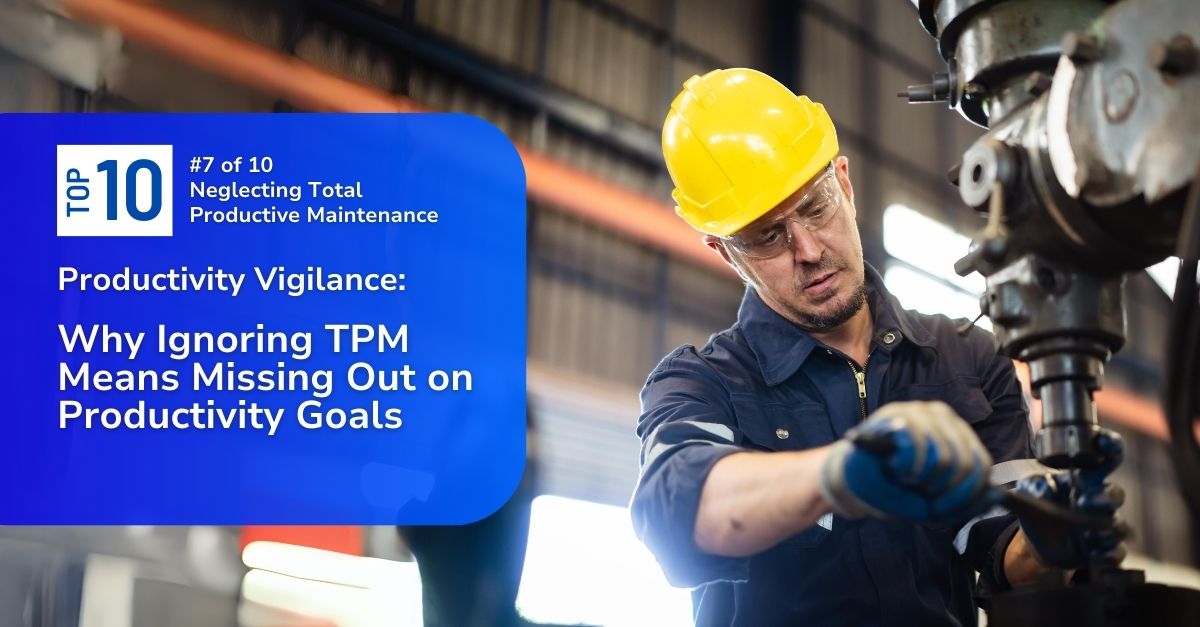
Total Productive Maintenance (TPM) is a critical pillar of manufacturing productivity, designed to optimize equipment efficiency and minimize downtime.
Despite its importance, many manufacturing facilities neglect TPM, leading to a cascade of negative effects throughout the production process.
One less common example of a secondary symptom of neglecting TPM is the increase in product defects and rework rates. When maintenance is inadequate, equipment often operates outside of critical tolerances, leading to inconsistencies in production processes. For instance, an uncalibrated machine might produce parts that do not meet specifications, resulting in higher defect rates. These defective products then need to be reworked or scrapped, consuming additional resources and time. This not only leads to higher production costs but also disrupts the production schedule, as more time is spent correcting errors rather than producing new goods. The increased defect and rework rates significantly reduce overall productivity as the focus shifts from efficient production to addressing quality issues.
By exploring the top 10 ways that neglecting Total Productive Maintenance negatively affects manufacturing productivity, we can better understand the granular issues faced by managers and develop strategies to mitigate these challenges. The focus will be on secondary symptoms—those indirect yet impactful consequences—that result from inadequate maintenance practices. Each point will delve into the specific productivity impacts and provide actionable steps for improvement, ensuring that your manufacturing operations remain smooth, efficient, and productive.
1 Ineffective CMMS Implementation:
A poorly implemented or underutilized Computerized Maintenance Management System (CMMS) can lead to inefficient maintenance scheduling, lack of data-driven insights, and missed preventive maintenance opportunities. Without proper utilization of CMMS, maintenance activities become reactive rather than proactive. This results in unexpected equipment failures and unplanned downtime, directly impacting productivity. Managers often struggle with incomplete or inaccurate data, making it difficult to prioritize maintenance tasks and predict equipment failures effectively.
Mitigation: To address this, ensure that the CMMS implementation is thorough and includes comprehensive training for all users. Regular audits of the system should be conducted to ensure data accuracy and completeness. Integration of CMMS with other enterprise systems can provide a holistic view of maintenance needs. Utilizing the full capabilities of CMMS, including predictive maintenance features, can help in scheduling preventive maintenance tasks effectively, thereby reducing unexpected equipment failures and improving overall productivity.
2Impact on Lean Initiatives:
Neglecting TPM can derail other lean manufacturing initiatives due to the inability to maintain stable and predictable production processes. Lean initiatives rely on the elimination of waste, which is impossible when equipment is unreliable and prone to breakdowns. Unplanned downtime disrupts the flow of production, leading to inefficiencies, increased lead times, and higher operational costs. This can nullify the gains from lean practices such as Just-In-Time (JIT) production and continuous improvement efforts.
Mitigation: Integrating TPM into lean manufacturing practices is crucial. Regular maintenance schedules should be aligned with production schedules to minimize disruptions. Cross-training employees on both lean principles and TPM can foster a culture of continuous improvement. Establishing clear communication channels between maintenance and production teams ensures that any maintenance issues are promptly addressed, maintaining the stability needed for lean initiatives to succeed.
3Understaffed Maintenance Department:
An understaffed maintenance department leads to reactive maintenance, delayed repairs, and overlooked preventive tasks. When there aren’t enough personnel to handle the maintenance workload, the focus shifts to fixing problems after they occur rather than preventing them. This reactive approach increases downtime and repair costs while reducing equipment availability and productivity. Maintenance staff may be forced to prioritize urgent fixes over routine maintenance, further compounding the issue.
Mitigation: Adequate staffing levels must be maintained to ensure both preventive and reactive maintenance can be effectively managed. Investing in workforce planning tools can help predict future staffing needs based on maintenance workload and production schedules. Additionally, outsourcing certain maintenance tasks during peak periods can alleviate the burden on internal staff. Ensuring a well-staffed maintenance department enables a proactive approach to maintenance, enhancing equipment reliability and productivity.
4Overburdened Maintenance Personnel:
Stretching maintenance staff too thin leads to burnout, errors, and neglect of critical TPM tasks due to overwhelming workloads. Overworked employees are more likely to make mistakes, overlook potential issues, and skip important maintenance steps. This not only compromises the quality of maintenance work but also increases the likelihood of equipment failures, directly affecting productivity. Burnout can result in high turnover rates, further exacerbating staffing issues and knowledge loss.
Mitigation: To prevent overburdening maintenance personnel, balancing workloads and providing adequate support is essential. Implementing a job rotation system can help distribute tasks evenly and reduce burnout. Encouraging a healthy work-life balance and offering mental health support can also mitigate the effects of stress and fatigue. Additionally, leveraging automation and technology, such as condition monitoring and predictive maintenance tools, can reduce the manual workload on maintenance staff, allowing them to focus on more critical tasks.
5Complexity in Production Scheduling:
Unreliable equipment can severely disrupt manufacturing processes by adding complexity and inefficiency to production scheduling. When equipment is prone to breakdowns, it becomes challenging to plan and stick to production schedules. This leads to frequent rescheduling, increased lead times, and higher inventory levels to buffer against uncertainties. The lack of predictability can frustrate production managers and create a chaotic working environment, negatively impacting overall productivity.
Mitigation: To mitigate these issues, predictive maintenance should be integrated into production scheduling. Using data analytics to predict equipment failures allows for maintenance to be scheduled during planned downtimes, minimizing disruptions. Collaboration between maintenance and production departments is crucial to develop realistic schedules that account for potential maintenance needs. Investing in more reliable equipment and continuously improving maintenance practices can also reduce the complexity of production scheduling, enhancing productivity.
6Poorly Maintained Tools and Equipment:
Worn-out or inadequate tools hinder maintenance effectiveness, prolong repair times, and contribute to equipment downtime. Poorly maintained tools can lead to subpar repairs, causing recurring issues and reducing the overall lifespan of equipment. This not only increases the frequency of maintenance interventions but also impacts the efficiency of production processes. Inconsistent maintenance quality results in frequent production stoppages, reducing throughput and increasing operational costs.
Mitigation: Regular inspection and maintenance of tools and equipment are essential. Implementing a tool management system can help track the condition and usage of tools, ensuring they are always in optimal condition. Providing maintenance personnel with high-quality tools and proper training on their use can improve repair quality and reduce downtime. Establishing a culture of proactive tool maintenance can enhance the effectiveness of maintenance tasks, leading to more reliable equipment and improved productivity.
7Inventory Management Issues:
Poorly managed or missing spare parts, consumables, or lubricants cause delays in repairs, extended equipment downtime, and lost production time. When necessary parts are not readily available, maintenance personnel cannot perform timely repairs, leading to prolonged equipment outages. This not only disrupts production schedules but also increases the cost of emergency part orders. Inadequate inventory management can also lead to overstocking, tying up capital and storage space unnecessarily.
Mitigation: Implementing a robust inventory management system is crucial to ensure the availability of necessary parts and consumables. Regular inventory audits and real-time tracking can help maintain optimal stock levels. Collaborating with suppliers to establish reliable supply chains and just-in-time delivery can reduce the need for large inventories while ensuring parts are available when needed. Training maintenance staff on inventory management practices can further enhance efficiency and reduce downtime.
8Lack of Training and Skill Development:
Insufficient training for both operators and maintenance personnel leads to missed opportunities for early issue detection, ineffective repairs, and equipment misuse. Without proper training, operators may not recognize early signs of equipment problems, resulting in minor issues escalating into major failures. Maintenance personnel lacking up-to-date skills may struggle with complex repairs, increasing downtime and reducing the effectiveness of maintenance activities. This lack of expertise directly impacts productivity by increasing the frequency and duration of equipment outages.
Mitigation: Investing in continuous training and skill development programs is essential. Regular training sessions should be conducted for both operators and maintenance personnel to keep them updated on the latest maintenance techniques and equipment usage. Implementing a mentorship program can facilitate knowledge transfer from experienced technicians to newer staff. Encouraging certifications and ongoing education can enhance the skill set of the maintenance team, leading to more effective repairs and better issue detection, thereby improving productivity.
9Aging and Obsolete Equipment:
Critical equipment that is past its prime or not regularly updated becomes unreliable, prone to breakdowns, and less efficient, hindering overall productivity. Aging equipment often requires more frequent repairs and is more susceptible to failures, leading to increased downtime and maintenance costs. The inefficiencies associated with obsolete equipment can slow down production processes, reduce product quality, and limit the company’s ability to meet market demands.
Mitigation: Regularly assessing the condition of equipment and planning for timely upgrades is essential. Establishing a capital investment plan for equipment renewal can help spread out the costs over time. Implementing a lifecycle management strategy ensures that equipment is replaced or upgraded before it becomes a liability. Additionally, adopting new technologies and innovations can improve equipment reliability and efficiency, leading to enhanced productivity and competitiveness.
10Inadequate Financial Planning:
Lack of investment in new equipment and technology due to poor financial planning leaves the company with outdated and inefficient assets, limiting growth and productivity potential. Insufficient funding for maintenance activities can lead to deferred maintenance, increasing the likelihood of equipment failures and extended downtime. Poor financial planning can also result in inadequate spare parts inventory and delayed maintenance activities, further exacerbating productivity issues.
Mitigation: Developing a comprehensive financial plan that includes regular investments in maintenance and equipment upgrades is crucial. Allocating a portion of the budget specifically for maintenance and technology improvements can ensure that funds are available when needed. Implementing a cost-benefit analysis for maintenance activities can help justify the necessary expenditures. Engaging financial experts to optimize budget allocation and planning can support sustained productivity improvements through well-funded maintenance initiatives.
Conclusion for Manufacturing Leaders
Neglecting Total Productive Maintenance (TPM) has far-reaching consequences that extend beyond immediate equipment failures and downtime. The secondary symptoms, such as ineffective CMMS implementation, impacts on lean initiatives, understaffed maintenance departments, overburdened maintenance personnel, complexity in production scheduling, poorly maintained tools and equipment, inventory management issues, lack of training and skill development, aging and obsolete equipment, and inadequate financial planning, all contribute to a significant decline in manufacturing productivity. Each of these issues creates a cascade of problems that disrupt production processes, increase costs, and reduce overall efficiency.
By focusing on these areas, manufacturers can enhance equipment reliability, reduce downtime, and improve the overall effectiveness of their operations.
How POWERS Can Help
The POWERS methodology can play a crucial role in overcoming these productivity challenges. By emphasizing the principles of Focused Improvement, Autonomous Maintenance, Planned Maintenance, Quality Maintenance, and Education and Training, POWERS provides a structured framework to enhance maintenance practices and boost productivity.
- Planned Maintenance: Scheduling maintenance activities during planned downtimes minimizes disruptions to production schedules. By anticipating maintenance needs and planning accordingly, manufacturers can avoid unplanned downtime and maintain a smooth production flow.
- Quality Maintenance: Ensuring that maintenance activities are performed to the highest standards reduces the risk of equipment failures and defects. High-quality maintenance practices contribute to longer equipment lifespans and more reliable production processes.
- Education and Training: Providing continuous training and skill development for both operators and maintenance personnel ensures that they are equipped to handle maintenance tasks effectively. This improves the quality of maintenance work and enhances early issue detection and problem-solving capabilities.
The POWERS AMP (Advanced Maintenance Performance) Program is an end-to-end solution designed to improve maintenance performance. It enhances both the tactical and technical aspects of maintenance, focusing on strategic approaches, resource management, and hands-on training in maintenance fundamentals. By improving the skills of the maintenance workforce, the AMP Program increases Overall Equipment Effectiveness (OEE), addressing bottlenecks in uptime, throughput, capacity, and quality.
By integrating the principles of POWERS and the AMP Program into their maintenance practices, manufacturers can significantly improve their productivity. The structured approach provided by POWERS helps address the secondary symptoms of neglecting TPM, leading to more efficient and reliable production processes. Embracing TPM and the POWERS methodology ensures that manufacturing operations remain competitive, productive, and capable of meeting market demands.
To learn how POWERS can transform your maintenance operations and boost productivity, contact them today.
- Speak to an Expert: Call +1 678-971-4711 to discuss your specific challenges and goals.
- Email Us: Get tailored insights by emailing info@thepowerscompany.com
- Request an Assessment: Use our online contact form, and one of our expert manufacturing consultants will reach out to schedule an in-depth analysis of your operations.
Continue Reading from this Mastery Series
- Part 1 – Without Top Talent, Top Productivity is Elusive
- Part 2 – How Blind Spots in Cost Analysis Hide Your Productivity Struggles
- Part 3 – When Supply Chain Issues Deliver A Productivity Hit
- Part 4 – Environmental Threats that Threaten Your Productivity
- Part 5 – Don’t Let Scaling Up Bring Down Your Productivity
- Part 6 – How Vulnerabilities to Disruptions Undermine Productivity
- Part 7 – Why Ignoring TPM Means Missing Out on Productivity Goals
- Part 8 – How Poor Training and Development Creates Productivity Shortfalls
- Part 9 – How Delayed NPIs Lead to Productivity Misses
- Part 10 – How Inaccurate Data Obscures Productivity Insight