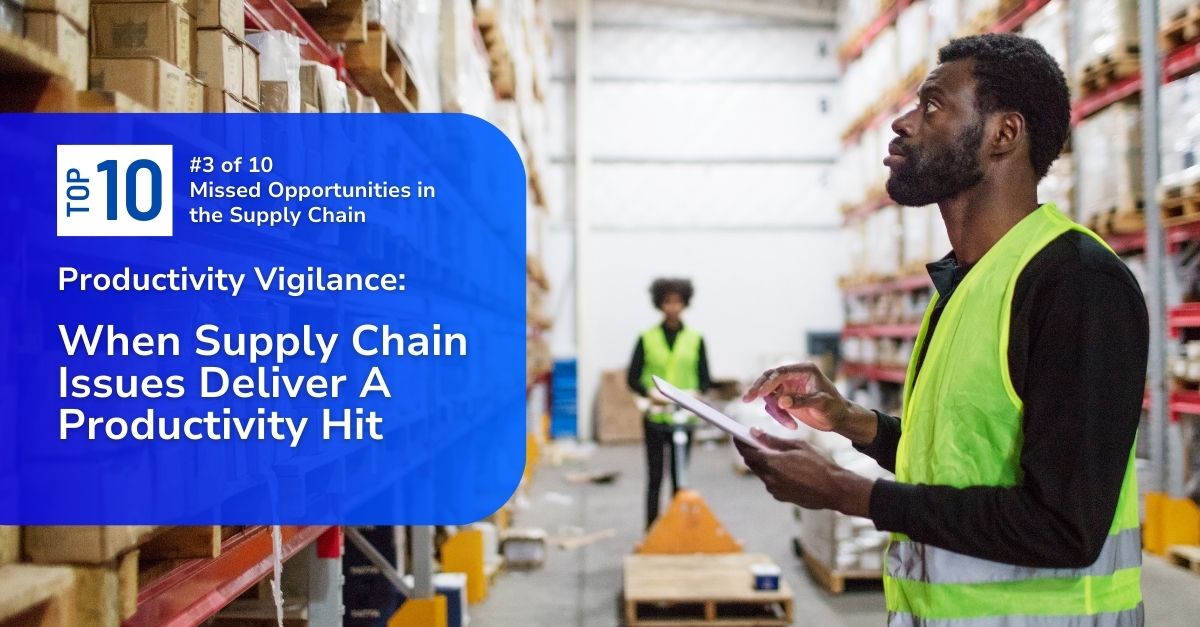
Every manufacturer strives to produce more high-quality products with the same—or even fewer—resources.
Missed opportunities in your sourcing, communication with suppliers, and internal inventory management don’t just cause isolated headaches; they have secondary consequences that ripple through your entire operation. Here’s how the fallout unfolds:
The production schedule is thrown into chaos, forcing teams to frantically locate substitute materials or overhaul production plans, wasting precious time and resources. In extreme cases, production lines may even grind to a halt, leaving workers and expensive machinery idle while critical components are awaited. This disruption ultimately jeopardizes customer deadlines, leading to dissatisfaction, eroded trust, and potential loss of future business.
This is just one example; seemingly minor oversights in your procurement processes have far-reaching implications for your manufacturing productivity. Let’s examine ten of the most common culprits silently undermining your shop floor’s output and, most importantly, provide solutions to regain control and boost your productivity.
1Outdated supplier contracts with unfavorable terms:
Seemingly acceptable contracts can hide problematic clauses related to pricing, lead times, minimum order quantities, or change procedures. These outdated terms significantly reduce your agility to adapt to shifts in demand, forcing you to absorb unexpected price hikes, face limitations on scaling production down, or experience manufacturing line stoppages due to lengthy change order protocols.
Mitigation: Proactively institute regular contract reviews with critical suppliers. Analyze real-world data from the past year against the agreed-upon terms to identify areas for negotiation and improvement. Focus on clauses that could negatively impact your flexibility.
2Inaccurate or incomplete bills of materials (BOMs):
Errors in your BOMs, from missing components to incorrect quantities or outdated part numbers, create a cascading series of disruptions. This leads to incorrect purchasing orders, frustrating last-minute searches for substitute components, and even production lines grinding to a halt due to missing materials. All of these scenarios waste valuable time and valuable resources.
Mitigation: Implement a stringent BOM change management process with version control, clear approval chains, and integration with your ERP system. This ensures real-time accuracy and minimizes the potential for costly errors.
3Inconsistent communication with suppliers:
Relying on sporadic phone calls or disorganized email threads for critical material orders and status updates is a recipe for miscommunication and costly delays. This lack of visibility into lead times and order progress leads to unexpected production delays and costly surprises.
Mitigation: Establish formalized communication protocols with key suppliers. This could involve scheduled weekly status calls, access to a shared supplier portal for visibility, or standardized status update forms with clear expectations on turnaround times for information.
4Over-reliance on spot buying instead of strategic sourcing:
Constantly scrambling for last-minute material purchases to avoid stockouts leads to rushed spot buying at inflated prices from potentially unreliable vendors. This results in budget overruns and inconsistent component quality that impacts production quality and drains team resources allocated to other key activities.
Mitigation: Develop a strategic sourcing plan that categorizes suppliers based on the criticality of materials. Proactively negotiate contracts, build relationships with preferred suppliers, and secure volume-based discounts for critical materials well in advance.
5Outdated or inaccurate inventory data:
Incorrect inventory records lead to a double-edged problem: excess inventory or unexpected stockouts. Excess stock ties up capital and warehouse space, while stockouts halt production lines and erode customer trust.
Mitigation: Invest in a robust inventory management system suited to your business needs. Conduct regular cycle counts and spot checks to verify stock accuracy. Implement regular system audits to ensure consistent data integrity.
6Single-sourcing of critical components without backup options:
Placing complete reliance on just one supplier for critical components means a disruption in their supply chain has a direct, immediate impact on your production. This leads to lost revenue, potential damage to customer relationships, and a frantic scramble to secure alternative sources.
Mitigation: Develop a comprehensive risk-assessment strategy for components, taking into account potential disruptions. Always qualify and maintain relationships with backup suppliers, understanding that this may involve slightly higher costs in exchange for the security of supply continuity.
7Lack of contingency plans for transportation disruptions:
Unexpected events like port congestion, weather delays, or carrier capacity issues can throw meticulously planned material deliveries into disarray. Without alternative transportation routes, pre-negotiated backup carriers, or contingency plans in place, you risk production slowdowns or stoppages while scrambling for solutions.
Mitigation: Develop a transportation risk management plan. Conduct scenario planning to identify potential disruptions and map out alternative routes and carriers. Proactively negotiate backup carrier rates when establishing primary transportation contracts.
8Unreliable supplier deliveries:
Inconsistent supplier performance with late or incomplete deliveries throws a wrench into your production schedules. This forces last-minute expediting costs disrupts production flow, and can result in missed customer deadlines.
Mitigation: Track supplier delivery performance with clear metrics (on-time, in-full percentages). Establish clear communication channels for proactive updates on potential delays. Implement a supplier qualification process that includes historical delivery reliability as a key factor.
9Lack of investment in supply chain technology:
Relying on manual spreadsheets or outdated systems for procurement, inventory tracking, and supplier management inhibits real-time visibility and data-driven decision-making. This leads to ruined productivity metrics, delayed responses to changes in demand, and missed opportunities for optimization.
Mitigation: Assess the current state of your supply chain technology. Research and invest in appropriate tools such as supplier portals, demand planning software, inventory management systems, or transportation management solutions. Start with high-impact areas while aligning with your overall business goals.
10Inaccurate forecasts impacting material planning:
Inaccurate forecasts create a ripple effect on your procurement, leading to either excess inventory or shortages. Both scenarios cause budget overruns, waste resources, and potentially halt production if critical materials aren’t available.
Mitigation: Invest in a demand forecasting solution that takes into account historical data, market trends, seasonality, and other relevant variables. Collaborate closely with your sales and operations teams to align forecasts with on-the-ground realities. Regularly review forecast accuracy and adjust models as needed for improvement.
Conclusion for Manufacturing Operations Leaders
The ripple effects of missed supply chain opportunities should not be underestimated. They drain resources, disrupt your shop floor, jeopardize customer relationships, and ultimately erode hard-earned profits. The solutions presented in this post offer attainable starting points to combat these insidious productivity killers.
How POWERS Can Help
At POWERS, we understand the unique challenges that manufacturers face in optimizing their supply chains. Through our deep industry expertise and proven methodologies, we provide customized solutions that don’t just address surface-level issues but drive sustainable improvements in productivity:
- Strategic Sourcing and Procurement: We help you build a resilient supplier network, negotiate favorable contracts, and implement data-driven procurement strategies for both cost optimization and supply continuity.
- Inventory Management Optimization: Our team analyzes your inventory data, identifies bottlenecks, and recommends the right solutions for improved accuracy and streamlined material flow.
- Technology Implementation and Integration: We guide you through selecting and implementing the most impactful supply chain tools, ensuring they align with your specific needs and seamlessly integrate with existing systems.
- Speak to an Expert: Call +1 678-971-4711 to discuss your specific challenges and goals.
- Email Us: Get tailored insights by emailing info@thepowerscompany.com
- Request an Assessment: Use our online contact form, and one of our expert manufacturing consultants will reach out to schedule an in-depth analysis of your operations.
Let us help you create a streamlined and robust supply chain that supports your manufacturing goals and boosts overall productivity and profitability.
Continue Reading from this Mastery Series
- Part 1 – Without Top Talent, Top Productivity is Elusive
- Part 2 – How Blind Spots in Cost Analysis Hide Your Productivity Struggles
- Part 3 – When Supply Chain Issues Deliver A Productivity Hit
- Part 4 – Environmental Threats that Threaten Your Productivity
- Part 5 – Don’t Let Scaling Up Bring Down Your Productivity
- Part 6 – How Vulnerabilities to Disruptions Undermine Productivity
- Part 7 – Why Ignoring TPM Means Missing Out on Productivity Goals
- Part 8 – How Poor Training and Development Creates Productivity Shortfalls
- Part 9 – How Delayed NPIs Lead to Productivity Misses
- Part 10 – How Inaccurate Data Obscures Productivity Insight