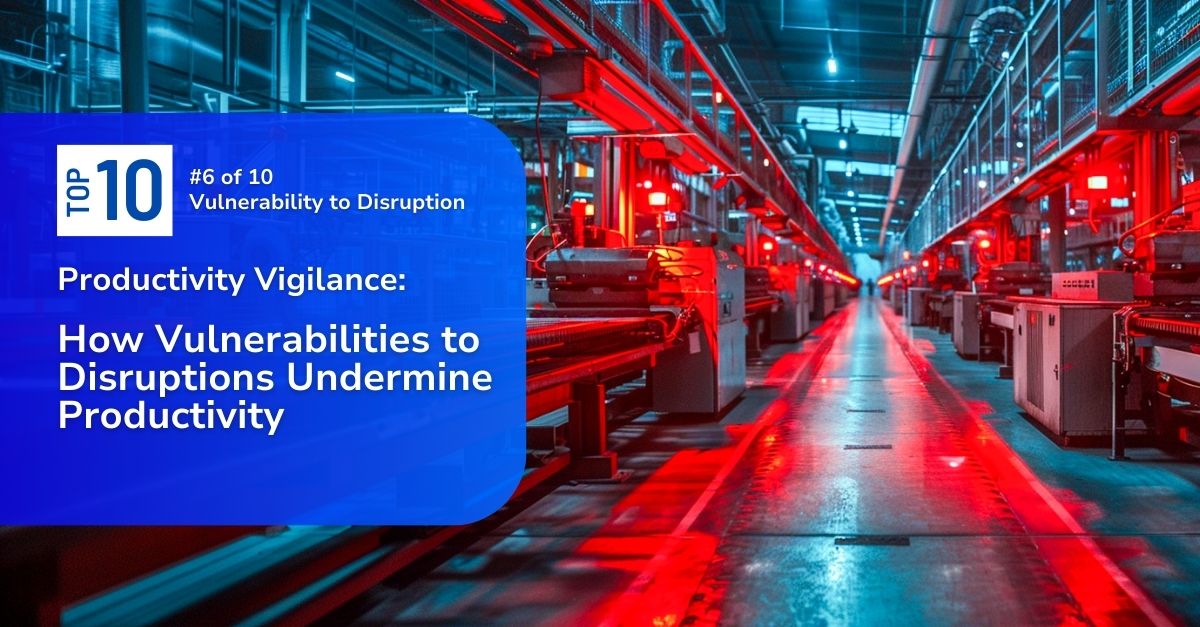
Sudden disruptions can wreak havoc on production lines, causing delays, inefficiencies, and financial losses. If not promptly addressed, shop floor managers encounter issues that can lead to significant productivity declines.
Consider a less common example: a niche manufacturer of custom aerospace components relies on a specialized alloy sourced from a single supplier in a politically unstable region. When geopolitical tensions escalate, the supplier faces export restrictions, halting the alloy’s shipment.
Without an alternative source, production grinds to a halt, leading to missed deadlines and lost contracts. This disruption affects immediate productivity and undermines the manufacturer’s reputation and long-term client relationships.
This example illustrates the broader impact of a sudden supply chain disruption on manufacturing productivity. This post delves into ten disruptions that are productivity killers and offering practical mitigation strategies for each.
By drawing from real-world experiences and credible sources, we aim to provide actionable insights to help manufacturers navigate these challenges effectively and maintain high productivity levels.
1Single Point of Failure Risk:
Relying heavily on specific individuals creates a single point of failure risk. When key personnel become unavailable due to illness, resignation, or other reasons, their absence can lead to significant disruptions. These individuals often hold critical knowledge and skills that are not easily transferable, causing production delays and errors. For example, a specialized technician’s unexpected absence can halt an entire production line, impacting deadlines and productivity.
Mitigation: To address this risk, manufacturers should implement a cross-training program to ensure that multiple employees can perform critical tasks. Additionally, documenting standard operating procedures (SOPs) and maintaining a knowledge repository can help transfer essential knowledge across the workforce. Companies can maintain continuity even when key personnel are unavailable by creating redundancy in skills and knowledge.
2M&A Integration Challenges:
Mergers and acquisitions often lead to integration challenges that disrupt operations, systems, and company culture. These disruptions can create confusion, miscommunication, and resistance among employees. Integration issues can slow down production processes, introduce inefficiencies, and negatively impact employee morale, all of which reduce overall productivity.
Mitigation: Effective integration planning is crucial to mitigate these challenges. Companies should develop a detailed integration roadmap that addresses cultural alignment, system interoperability, and process harmonization. Engaging employees early in the process and providing clear communication about changes can ease the transition. Additionally, assigning dedicated integration teams to manage the process ensures that disruptions are minimized and productivity is maintained.
3Untested Implementation:
Introducing new technology or procedures without thorough testing can lead to unexpected problems. Untested implementations often result in system failures, process inefficiencies, and production stoppages. For instance, deploying new manufacturing software without proper testing can cause data inaccuracies and operational delays, significantly affecting productivity.
Mitigation: To prevent these issues, manufacturers should adopt a phased implementation approach that includes rigorous testing and pilot programs. This allows companies to identify and address potential problems before full-scale deployment. Involving end-users in the testing process can provide valuable feedback and ensure the new system meets operational needs. Additionally, providing comprehensive training to employees on the new technology or procedures can facilitate a smoother transition.
4Geopolitical Supply Chain Disruptions:
Geopolitical events or conflicts can destabilize previously reliable supply sources, leading to supply chain disruptions. These disruptions can cause delays in receiving critical materials, increasing lead times and production costs. For example, trade restrictions or political instability in supplier regions can halt the flow of essential components, forcing manufacturers to pause production and scramble for alternatives.
Mitigation: To mitigate geopolitical supply chain risks, manufacturers should diversify their supplier base to avoid over-reliance on a single source. Establishing relationships with multiple suppliers in different regions can provide alternative options in case of disruptions. Additionally, maintaining strategic stockpiles of critical materials can buffer against short-term supply chain interruptions. Regularly assessing geopolitical risks and developing contingency plans can also help companies respond quickly to unforeseen events.
5Regulatory Compliance Challenges:
Regulatory compliance challenges are a common disruption in manufacturing. Unexpected changes in laws or regulations can require rapid adaptations to maintain compliance. These abrupt shifts often lead to increased administrative workload, production delays, and financial penalties. For instance, new environmental regulations may necessitate changes in manufacturing processes, which can halt production lines as adjustments are made. This disrupts the workflow, causing delays and reducing overall productivity.
Mitigation: To mitigate regulatory compliance challenges, manufacturers should invest in a robust compliance management system. This system should include continuous monitoring of regulatory updates, regular compliance audits, and staff training programs. By staying proactive, companies can anticipate changes and implement necessary adjustments before they disrupt operations. Additionally, engaging with industry associations can provide early warnings of upcoming regulatory changes, allowing for better preparation.
6Critical Equipment Failure:
Sudden breakdowns of essential machinery can cause immediate production stoppages, leading to significant productivity losses. Equipment failures often result from inadequate maintenance, aging infrastructure, or unexpected technical issues. These breakdowns not only halt production but also incur repair costs and potential delays in meeting customer orders.
Mitigation: Implementing a proactive maintenance program is key to preventing equipment failures. Regular inspections, predictive maintenance technologies, and timely repairs can extend the lifespan of machinery and reduce the likelihood of unexpected breakdowns. Investing in modern, reliable equipment and training staff on proper operation and maintenance procedures can further enhance productivity by minimizing downtime.
7Supply Chain Vulnerabilities:
Running out of vital materials or components without a secondary source can halt production. Supply chain vulnerabilities arise from over-reliance on a single supplier or inadequate inventory management. When essential materials are unavailable, production lines come to a standstill, delaying order fulfillment and reducing productivity.
Mitigation: To mitigate supply chain vulnerabilities, manufacturers should implement robust inventory management practices and develop a network of reliable suppliers. Utilizing technologies such as demand forecasting and inventory optimization software can help maintain optimal stock levels. Establishing strong relationships with multiple suppliers ensures access to critical materials even if one source fails. Regularly reviewing and updating supply chain strategies can also enhance resilience and productivity.
8Catastrophic Events:
Major accidents, natural disasters, or unforeseen incidents can cause significant damage and operational downtime. Catastrophic events such as fires, floods, or industrial accidents can destroy infrastructure, disrupt supply chains, and halt production for extended periods. The aftermath of such events often involves costly repairs, lost production time, and a lengthy recovery process, severely impacting productivity.
Mitigation: To mitigate the impact of catastrophic events, manufacturers should develop comprehensive disaster recovery and business continuity plans. These plans should include risk assessments, emergency response procedures, and strategies for maintaining operations during and after a crisis. Investing in resilient infrastructure and implementing safety measures can reduce the likelihood of accidents and minimize damage. Regularly conducting drills and training employees on emergency protocols ensures preparedness and swift recovery.
9Underprepared Leadership:
Promoting staff into leadership positions without adequate skills or experience can lead to poor decision-making and operational inefficiencies. Underprepared leaders may struggle to manage teams effectively, resulting in miscommunication, low morale, and declines in productivity. For example, a new manager lacking experience in production planning may make scheduling errors, causing delays and disruptions on the shop floor.
Mitigation: To address this issue, companies should invest in leadership development programs that equip potential leaders with the necessary skills and knowledge. Mentoring and coaching from experienced managers can provide valuable guidance and support. Regular performance evaluations and feedback can help identify areas for improvement and ensure leaders are prepared for their roles. Promoting a culture of continuous learning and development fosters effective leadership and enhances overall productivity.
10Prioritization Disruptions:
Abruptly changing production schedules to favor certain clients can cause unforeseen delays for others. Prioritization disruptions often occur when companies shift resources and focus to meet urgent demands, neglecting other orders. This leads to production bottlenecks, extended lead times, and dissatisfied customers, ultimately affecting productivity and reputation.
Mitigation: To mitigate prioritization disruptions, manufacturers should implement flexible production scheduling systems that can adapt to changing demands without causing delays. Clear communication with clients about lead times and potential delays can manage expectations and reduce pressure on production schedules. Utilizing advanced planning and scheduling software can optimize resource allocation and ensure balanced prioritization of orders. Establishing a collaborative approach with clients to understand their needs and constraints can also improve planning and productivity.
Conclusion for Manufacturing Leaders
Manufacturers can unlock significant productivity gains by acknowledging and strategically addressing these hidden vulnerabilities. The insidious nature of these secondary symptoms necessitates a proactive and vigilant approach, one that emphasizes early detection and swift mitigation.
How POWERS Empowers Your Productivity
- Proactively plan for potential disruptions and seasonal variations, ensuring smooth operations even in the face of unexpected challenges.
- Organize your resources – both human and technological – to maximize efficiency and minimize bottlenecks.
- Optimize workflows to streamline processes, eliminate redundancies, and enhance overall productivity.
- Evaluate performance regularly, using data-driven insights to identify areas for improvement and track progress toward your goals.
- Review your strategies and adapt them as needed to ensure continuous improvement and stay ahead of the competition.
- Standardize processes and procedures to reduce variability, minimize errors, and maintain consistent quality output.
By embracing the POWERS methodology and remaining vigilant against the hidden threats to productivity, you can transform your manufacturing operations into a well-oiled machine capable of achieving sustained growth and success in today’s dynamic business landscape. Remember, productivity is not a destination but a journey, and the POWERS methodology is your roadmap to navigate it successfully.
- Speak to an Expert: Call +1 678-971-4711 to discuss your specific challenges and goals.
- Email Us: Get tailored insights by emailing info@thepowerscompany.com
- Request an Assessment: Use our online contact form, and one of our expert manufacturing consultants will reach out to schedule an in-depth analysis of your operations.
Continue Reading from this Mastery Series
- Part 1 – Without Top Talent, Top Productivity is Elusive
- Part 2 – How Blind Spots in Cost Analysis Hide Your Productivity Struggles
- Part 3 – When Supply Chain Issues Deliver A Productivity Hit
- Part 4 – Environmental Threats that Threaten Your Productivity
- Part 5 – Don’t Let Scaling Up Bring Down Your Productivity
- Part 6 – How Vulnerabilities to Disruptions Undermine Productivity
- Part 7 – Why Ignoring TPM Means Missing Out on Productivity Goals
- Part 8 – How Poor Training and Development Creates Productivity Shortfalls
- Part 9 – How Delayed NPIs Lead to Productivity Misses
- Part 10 – How Inaccurate Data Obscures Productivity Insight