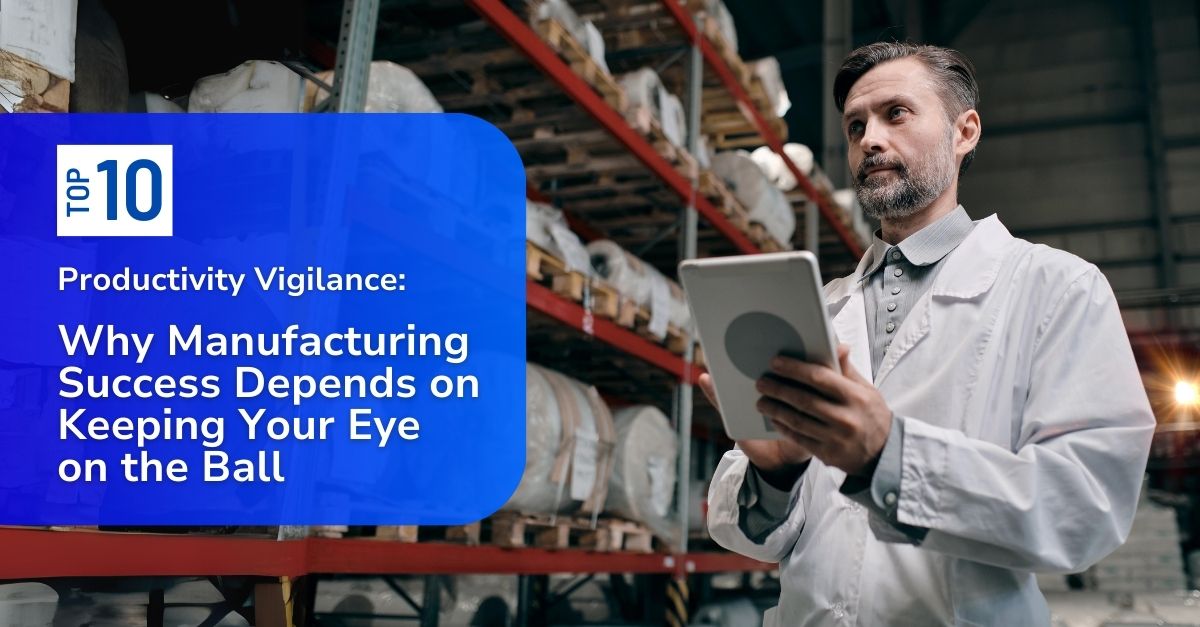
Productivity is a crucial indicator of manufacturing operational health. But productivity is more than just efficiency. Efficiency focuses on doing things right – minimizing waste and maximizing resource usage.
In manufacturing, productivity typically involves measuring output (goods or services produced) in relation to inputs like labor hours, capital, and materials invested.
A dip in productivity is not just a minor setback. It’s a clear sign that your manufacturing processes are not delivering optimal output relative to the resources consumed.
Neglecting this issue can have severe consequences, affecting everything from profitability to your ability to meet customer expectations. Let’s now explore the top 10 dangers of low productivity and how to tackle them.
1Inability to Attract Top Talent:
In today’s skilled labor shortage, manufacturers can’t afford to be seen as inefficient or behind the technological curve. Top talent seeks out employers with modern, streamlined operations. Low productivity signals outdated processes, potentially deterring the best candidates and leaving you with a less skilled workforce.
2Blind Spots in Cost Analysis:
Without accurate productivity metrics, manufacturers can severely underestimate their actual cost per unit. This can lead to underpricing products (eroding profits), overpricing them (losing bids), and misidentifying areas needing cost-reduction initiatives.
3Missed Opportunities in the Supply Chain:
Manufacturers with low productivity are less reliable partners in the supply chain. Unpredictable output and inconsistent lead times can strain relationships with suppliers and distributors. This can result in higher procurement costs, stockouts, and potential disruptions in your ability to meet customer orders.
4Environmental Impact:
Inefficient use of resources is a hallmark of low productivity. Wasted energy, increased scrap, and higher emissions contribute to a larger environmental footprint. This can put you at odds with sustainability-focused customers and even lead to non-compliance with environmental regulations.
5Difficulty Scaling Production:
Inflexible processes caused by low productivity make it nearly impossible to scale production when demand surges rapidly. This inability to capitalize on market opportunities leads to lost revenue and leaves you vulnerable to competitors who can ramp up output quickly.
6Vulnerability to Disruption:
Low productivity leads to a less resilient operation. As the pandemic highlighted, companies with lean, optimized operations are better equipped to withstand disruptions. Those with lagging productivity are more likely to experience severe production delays, supply shortages, and an inability to adapt to sudden market shifts.
7Neglecting Total Productive Maintenance (TPM):
Flagging productivity often indicates insufficient emphasis on proactive maintenance. Without TPM’s focus on operator-driven upkeep, equipment reliability suffers. Increased downtime and unplanned maintenance further erode productivity and drive up costs.
8Lost Training Investment:
Skills training wastes resources if inefficient processes, faulty equipment, or a lack of standardization hinder employees from developing and utilizing their newly acquired skills. Low productivity can render training ineffective, limiting employee development and perpetuating a cycle of operational stagnation.
9Delayed New Product Introductions (NPI):
Low productivity lengthens every stage of NPI, from design and prototyping to production ramp-up. This sluggish pace hinders your ability to capitalize on emerging trends, potentially resulting in competitors beating you to market and capturing demand.
10Data Inaccuracy:
Without consistent productivity tracking, data on machine output, labor hours, and waste is likely unreliable. This skewed data leads to poor forecasting, misinformed investments, and a misplaced focus on improvement efforts, hindering your ability to make truly impactful changes.
Proactive Strategies: Powers for Productivity Growth
At POWERS, we empower manufacturers to conquer these challenges and boost productivity. Here’s how we can help:
- Leadership Development: Transform frontline managers into change agents capable of inspiring and empowering teams.
- Process Optimization: Identify and eliminate wasteful practices with proven Lean Manufacturing methodologies.
- Advanced Maintenance Performance (AMP): Prevent downtime and keep your machines running at their best.
- Shop Floor Excellence: Upskill your workforce to spot and solve productivity bottlenecks at the source.
- Culture Performance Management (CPM): Create a data-driven culture focused on continuous improvement.
The Path Forward
Flagging productivity is not inevitable; it’s a sign that immediate action is needed. By proactively addressing productivity pain points with POWERS’ solutions, your manufacturing operations can achieve greater efficiency, resilience, and long-term success. Rest assured, with POWERS, you’re on the path to a more productive future. Contact us today to begin your productivity improvement journey.
- Call: +1 678-971-4711
- Email: info@thepowerscompany.com
- Form: Request Assesment